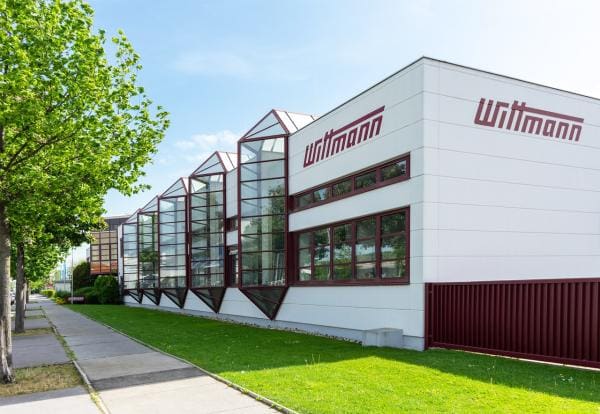
Wittmann Leads on Energy and Cost-Efficiency
Energy and materials-minded moulders are turning to Wittmann-based technology to squeeze optimum value from these important production factors.
Last October’s K Show gave proof that the circular economy and the focus on energy costs are business factors that are here to stay: Dan Williams, Wittmann Battenfeld UK Joint MD, says, “as ever, we are fortunate that Wittmann engineers and designers are addressing these needs head-on. In materials handling, for example, our latest Gravimax blenders ensure that polymer regrind can be automatically and easily integrated into existing processes, reducing virgin material to a minimum.”
Newly designed actuators for the Gravimax dosing flaps also mean that servicing expenses for this equipment can be almost completely dispensed with. Injection moulding applications with material throughputs of up to 700 kg/h are able to benefit from all of these Gravimax features.
Wittmann has developed the SpeedDrive pump for ultimate energy efficiency in mould temperature control. Typically paired with the company’s best-selling Tempro Plus D series of controllers, SpeedDrive aims to achieve maximum energy efficiency in an area of the plastics processing industry with particularly high energy consumption. The advantage of a SpeedDrive pump is that it allows for a freely selectable pump speed in order to adjust the pump operating point to the ongoing process.
Dan says that “our next Innovations magazine will also detail the advances Wittmann has made in parallel rather than the serial distribution of flow quantity can optimize the flow quantity – and deliver large savings.” He adds that “continual innovations such as these keep our Gravimax, Feedmax, and Tempro brands thriving with each passing year.”
Tracy Cadman, Wittmann Battenfeld UK Joint Managing Director, points out that “the wide range of Wittmann ancillary equipment is designed to save a variety of customers time and cost. We realise that just one kind of ancillary solution will not serve everyone. We, therefore, encourage the injection moulding market to test us on our tailor-made approach to ancillary equipment. Our product portfolio has cost-efficient materials handling and temperature controllers for most production needs and circumstances.”
Read more about Wittmann Battenfeld here.
Wittmann
01933 275777
Website
Email