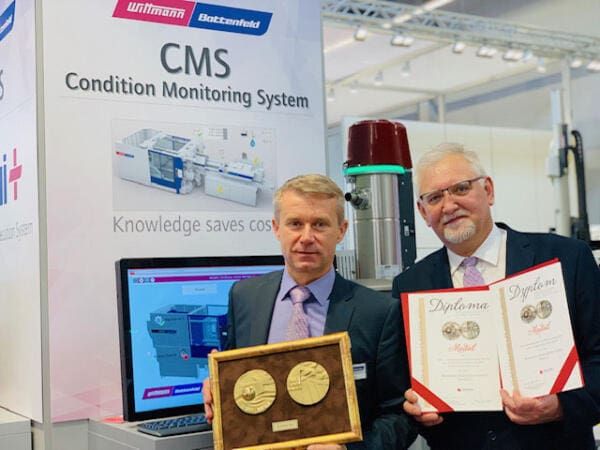
WITTMANN BATTENFELD Wins Award for Condition Monitoring System
At this year’s Plastpol in Kielce, WITTMANN BATTENFELD was able to convince an independent panel consisting of experts from universities and specialist institutes of the benefits offered by its condition monitoring system (CMS) when used in injection moulding machines for processing plastics.
Condition monitoring systems have already been used in large-scale plants for many years to anticipate and prevent production failures and optimise time-consuming servicing schedules. Recent progress in sensor technology and the increasing availability of high-speed data transfer networks now make such systems an interesting option for injection moulding machines, too. When used in injection moulding machines, the system monitors the condition of individual machine components to optimise their availability and efficiency and to keep them on this optimal level. The system detects malfunctions before they cause a machine breakdown and thus enables proactive scheduling of servicing sessions. In this way, costs can be minimised with a simultaneous increase in productivity.
The heart of the condition monitoring system is the CMS computer. This computer is part of a production control system. It communicates with the injection moulding machines and collects and saves the measurement data for possible later backtracking. A CMS control centre can monitor up to 50 machines simultaneously and pass on early warnings to the corporate maintenance staff by email. Besides current status information, the software also delivers trends indicating changes in functional values, which provide the basis for decision-making by maintenance staff.
At this year’s Plastpol, the condition monitoring system was demonstrated on a high-speed machine for the packaging industry, an EcoPower Xpress 160/1100+. On this machine, a lid made of PP (supplied by Borealis, Austria) was manufactured with a 4-cavity mould, using a high-speed IML system with a W837 pro-side-entry robot from WITTMANN.
Wittmann Battenfeld
+44 (0)1933 275777
Website
Email