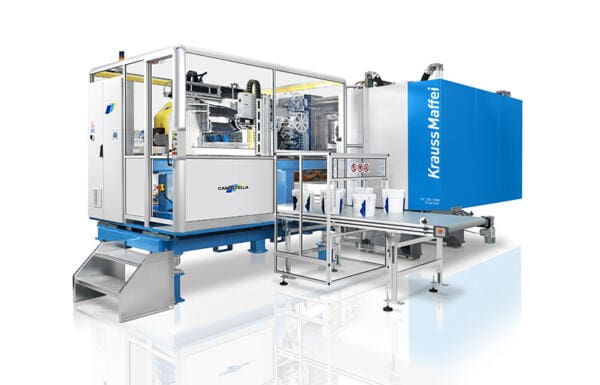
Predestined for Larger Packaging and Logistics Applications: The New KraussMaffei GX 1100 is here
The hydraulic GX series from KraussMaffei masters packaging as well as medical technology and automotive. The GX 1100, the new heavyweight of the series, sees its market launch at the K 2019 trade show.
“With the new clamping force size of 11,000 kN, we are expanding the range of our successful GX series with a specific target. We see great opportunities, particularly in the areas of packaging and logistics,” explains Hans-Ulrich Golz, President of the Injection Molding Machinery segment of KraussMaffei. The most recent member of the GX series has the well-known space-saving two-platen design, the GearX and GuideX clamping elements, the modular configuration and a wide variety of equipment options, for example, the particularly energy-saving BluePower servo drive.
The trade show application of the GX 1100-12000 at K itself is something special. Buckets of polypropylene with a capacity of 20 litres each are injected in two cavities and decorated by in-mould-labelling (IML). The shot weight is about 1500 grams with a cycle time of just 14 seconds. The available speed option ensures outstandingly fast injection speeds (up to 700 mm/s depending on the injection unit) as well as fast clamping movements. “We thus offer our customers an additional option to improve their opening and closing movements of the GX machine, especially for large packaging opening widths of more than 350 mm”, adds Golz. The dry cycle time is reduced by almost half a second. The benefit comes clear when calculating with 8000 production hours a year – in total, almost 130,000 buckets can be produced with the speed option.
The HPS barrier screw for polyolefins that are used here allows for particularly fast-melting and high shot weights thanks to the high L/D ratio of 26. The HPS barrier screws deliver a plasticising performance of up to 40% higher than the conventional high-performance screws from KraussMaffei.
Digital services control the entire manufacturing process
Digital services control and monitor the entire manufacturing process of the IML buckets. The APC Plus machine function ensures extreme consistency in component weight and thus high product quality by controlling the changeover point from injection pressure to holding pressure, as well as the holding pressure level, from shot to shot. Additionally, the dwell time of the polypropylene in the plasticising unit is monitored for the first time, which ensures a high material quality.
The DataXplorer, in turn, provides a detailed view of the depth of the process by storing up to 500 signals every five milliseconds as continuous graphs—for instance, signals from the machine itself or special signals such as the mould cavity pressure. The digital information from the injection moulding process and the information from the automation and peripherals flow converge in a new data collection point, which enables the customer to control and monitor its production flow specifically. Connection to an MES system is also possible.
Premiere for Smart Operation
The GX 1100 at the K trade show is the first KraussMaffei machine equipped with the Smart Operation control option of the product brand NETSTAL. Presented at the Fakuma 2018 trade show, the function allows for a separation between the application development and the later operation of the machine in production. The user benefits from a simplified operation and further increases in the efficiency of its production system. “The integration of Smart Operation into the KraussMaffei machine portfolio is an excellent reference for how we use synergies together to increase the added value of our customers. We will further advance this in the future,” says Golz.
Visit KraussMaffei at K Show 2019: Hall 15, Booth C24-C27
KraussMaffei
+44 (0) 1925 644100
Website
Email