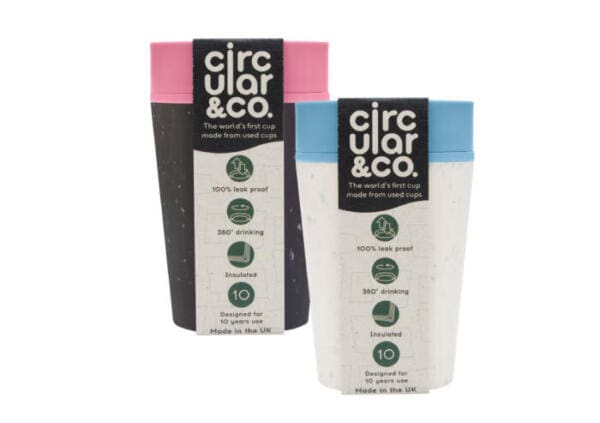
Polymermedics and Wittmann Battenfeld UK Help Bring the Coffee Break Home
With help from Wittmann Battenfeld UK, Cornwall-based technical injection moulder, Polymermedics Ltd, is bringing the production of sustainable coffee cups back to the UK from China.
An environmental success story – that supports British Manufacturing
With over 35 years’ experience delivering high quality technical plastic injection mouldings and assemblies, Polymermedics Ltd was the natural partner of choice when an opportunity arose to assist fellow Cornish business, Circular & Co, based in Perranporth.
Company founder Dan Dicker, formerly a designer with Dyson, had designed the revolutionary Circular Cup, a reusable coffee cup made from used paper coffee cups and plastic lids. Production had been based in China but – with Wittmann Battenfeld UK’s assistance – both Cornish businesses decided to start up production in the UK.
Polymermedics Operations Director, Neil Skyba, commented: “After many discussions, Circular & Co decided to go with Polymermedics. We liked the project as it was something a little different for us, and also the concept of using recycled coffee cups and plastics to make a reusable product was something we really wanted to get involved in. It’s great to be also be involved in a local project that has a great background story.”
An all-in-one solution required
The principal Polymermedics need was for an all-in-one production cell solution from a one-stop-shop supplier. Neil Skyba continued: “Our shop floor did not have existing capacity using a machine with the correct tonnage. We also needed a robot to aid with the downstream operations.”
Shop floor space limitations were also a factor: “The small footprint of the Wittmann Battenfeld was therefore ideal for us,” says Skyba. “It is a full one metre shorter and also slightly narrower than any alternative supplier. The fact that Wittmann Battenfeld UK could offer the robot and machine together as a single package and deliver it quickly also really helped. We had been looking at Wittmann Battenfeld technology for quite some while – and this opportunity provided the perfect project to take that leap.”
Adrian Walters, WIBA UK Area Sales Manager said: “From the get-go, it was a delight to work on this project and with Polymermedics. Plastic materials have had such an unfair and bad press for so long that it was very satisfying to help create a positive environmental success story – and one that also backs Britain as well.”
In the course of the project, Polymermedics was supplied with a Wittmann Battenfeld SmartPower 240/1000 injection moulding machine, a Wittmann Primus 16/Z2000/Y1200/X620 robot; a guarded cell, a conveyor and also five days of training with the equipment and the overall system. Walters adds: “We also retrofitted a second pump to the machine to give parallel movements of ejectors & cores.”
Neil Skyba praised the service from Wittmann Battenfeld throughout the project: “Adrian had the initial quote to us very quickly. Responses to additional questions and the barrel swap and additional pump were all handled very quickly and efficiently since WIBA UK knew that we needed the machine quickly.
“Fast response, quick answers to technical questions and the delivery of a good machine were all part and parcel of the order.”
Skyba adds: “This particular project uses recycled paper coffee cups in the resin. However, we did not need a special barrel or screw as it is fit to run in a standard machine. We also needed a good platen size as there are multiple tools that run in this machine. Ease of tool change was a big factor, and the machine did not let us down.”
Taking its place in a world-class manufacturing environment
With a comprehensive range of injection moulding machines, Polymermedics Ltd has lately gone from strength to strength and has the flexibility to fulfil diverse scope industries and customers.
One indication of the company’s confidence and versatility is the proven excellence of the mould shop and the manufacturing systems deployed there. The facility runs 24 machines, ranging from 5 to 240 tonnes, 24/7. This means that customers can be provided with an end-to-end total plastic injection moulding service, Polymermedics moulds, quality checks, assembled and sterilised before shipping to destinations all over the world.
The new Circular Cup project and the Wittmann Battenfeld production cell will take its place in a world-class manufacturing environment. At its peak, Polymermedics produces in excess of 40,000,000 components a week. The company maintains an average Overall Equipment Effectiveness of over 85%. This is already seen as world-class within the industry, and the Continuous Improvement (CI) aim at the St Austell facility is always to achieve higher.
Recent investment in new projects such as the Circular Cup has enabled Polymermedics Ltd to increase the output per head at the company. The technical advances now including new full hot runner tooling in order to increase effectiveness levels even higher. Such efficiencies lead to even shorter lead times, thus creating capacity for new projects coming online.
Wittmann Battenfeld
+44 (0)1933 275777
Website
Email