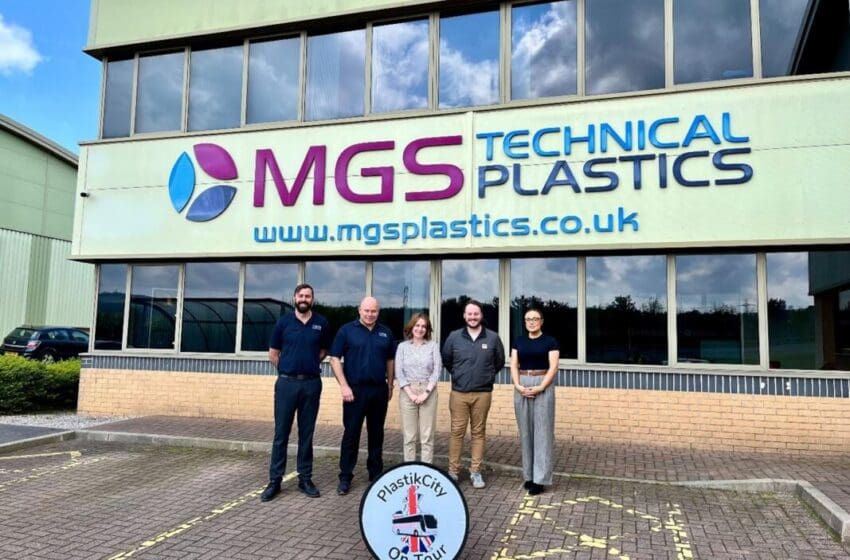
PlastikCity on Tour – MGS Technical Plastics
Getting your Trinity Audio player ready...
|
(Judson Smythe, Mark Preston, Jess Clarke, Will Clarke, Chloe Maine- Pictured above left to right)
Our next stop was Lancashire, where we visited MGS Technical Plastics, a leading plastic injection moulding company based in Blackburn. Established in 1974, MGS Technical Plastics has grown into a distinguished name in the industry, renowned for its expertise in volume manufacturing and its commitment to quality, sustainability, and community engagement.
MGS Technical Plastics started as a family-run business nearly five decades ago and has continually evolved to meet the demands of a dynamic market. The company moved to its current site at Centurion Business Park in Blackburn in 2013, a location that now houses both its offices and a state-of-the-art manufacturing facility. This move marked a significant milestone, enabling MGS to expand its capabilities and streamline operations under one roof.
The company’s leadership team has played a pivotal role in its success. All directors, including Judson as the Technical Director and Mark as the Sales Director, have risen through the ranks, beginning their careers as apprentices. Their deep technical knowledge and hands-on experience have been instrumental in driving the company’s growth and maintaining its competitive edge. This strong foundation in practical skills has fostered a culture of continuous improvement and professional development across the organisation.
Investment and Growth
MGS Technical Plastics has consistently invested in new technologies and equipment to enhance its manufacturing capabilities. Over the past few years, the company has invested over £3 million in advanced machinery and digital systems, including the integration of Industry 4.0 technologies. These investments have significantly increased their production efficiency and capacity.
The company boasts a range of injection moulding machines, from 35 to 900 tonnes, which allows it to handle projects of various sizes and complexities.
Recently, MGS added robots, a 3D printer, and an overhead crane to their facilities, further bolstering their production capabilities and enabling them to take on more complex and high-volume projects. The company’s forward-thinking approach ensures it remains at the forefront of technological advancements in the injection moulding industry.
Quality and Sustainability
Quality is at the heart of MGS Technical Plastics’ operations. The company’s quality assurance procedures are robust, supported by its IATF16949 accreditation, which is the latest recognised international quality standard for the automotive sector. This accreditation underscores a commitment to maintaining the highest standards and continually improving processes to meet the stringent requirements of their automotive clients.
In addition to quality, sustainability is a core value at MGS. The company takes a proactive approach to environmental responsibility, focusing on reducing waste, recycling plastics, and optimising production processes to minimise their carbon footprint at source as much as possible.
MGS is also pioneering the use of recycled materials and sustainable alternatives such as gum-tec and other biodegradable plastics. MGS encourages all team members to make ethical and environmentally conscious decisions, fostering a culture of sustainability throughout the organisation. This is underlined by its commitment to operating modern and energy-efficient machinery, and with a large solar PV installation on the factory roof providing a significant percentage of the site’s electricity from solar energy, the company is aiming to become certified as ‘Net-Zero’ in the future.
Part of this commitment to sustainability has transformed the processes inside the factory too. Now a paperless factory, jobs and workloads are managed digitally using industry 4.0 monitoring software, improving efficiencies and enabling greater data gathering for further analysing and improving performance over time.
The factory has also recently been fitted with motion-sensitive LED lighting and with the average age of its moulding machines less than 5 years old, there is no doubt that MGS’s growth plans have transformed its factory into a modern and digitally empowered industrial environment.
Community Engagement
MGS Technical Plastics is deeply committed to its local community. The company’s Managing Director actively participates in local regeneration projects, and many employees engage in charitable activities, from fundraising to participating in community challenges. The team at MGS is known for its enthusiastic participation in local events, reflecting their dedication to giving back to the community that has supported them over the years.
The company also places a strong emphasis on education and industry stewardship. They regularly collaborate with local schools and colleges to inspire the next generation of engineers and technicians.
By speaking at educational institutions and hosting factory tours and visits, MGS aims to demystify the plastics industry and highlight the benefits of UK manufacturing. This outreach is particularly important in countering the negative perceptions of plastics and promoting a balanced understanding of its essential role in modern life.
From a personal point of view, it was fantastic to see a manufacturer take it upon themselves to take such an active role in industry stewardship. It can sometimes feel like a losing battle, discussing the plastics industry and manufacturing in general with the younger generation, but through work like this done by MGS, together we can help to inspire the next generation of engineers.
Ambitious Plans for the Future
Looking ahead, MGS Technical Plastics has ambitious plans for growth and development. The company has recently acquired a second premises adjacent to its current site, which will be used to increase its finished goods capacity and support further expansion. With increased floorspace also comes the opportunity to reorder and optimise workflows, a process that will further increase MGS’s manufacturing capacity.
Despite recent challenges, such as the need to relocate a major water main to allow building expansion, the company remains focused on extending its facilities and enhancing its manufacturing capabilities over the next few years.
The company’s five-year plan includes continued investment in new machinery, improving in-house tooling capabilities, and further upgrading its digital systems with tools like Intouch Monitoring. These enhancements will allow MGS to maintain its high standards and continue delivering exceptional service to its clients.
Moreover, MGS is celebrating its 50th anniversary this year, a significant milestone that they plan to mark with various events and initiatives. This celebration not only acknowledges their rich history but also sets the stage for future achievements and continued success in the industry.
Interview with MGS Technical Plastics Team
Thank you for taking the time to speak with us today. To start, could you tell us a bit about the recent changes and investments at MGS Technical Plastics?
Judson: “Certainly. We’ve recently made significant investments in our machinery and technology, exceeding £3 million. This includes the addition of robots, a 3D printer, and an overhead crane. These investments have significantly boosted our production capabilities and efficiency. We’ve also expanded our site by acquiring an additional building for our finished goods, which has allowed us to optimise our workflows and plan for future growth.”
That sounds impressive. Can you tell us more about your target markets and the sectors you are involved in?
Mark: “We have a strong presence in the automotive sector, which accounts for about 30-50% of our business. Additionally, we operate in the hygiene, electrical, construction, retail, and health & safety sectors. We are also aiming to grow our client base in the aerospace, defence, and electric vehicle markets, which we see as highly technical growth areas.”
What are some of the key products and services that MGS offers?
Judson: “We specialise in the manufacture of injection moulded components. Beyond that, we offer a range of additional services such as pad printing, ultrasonic welding, chroming and plating, and insert moulding. Our ability to handle difficult materials, like PEEK and flexible PVC, sets us apart from many of our competitors. Recently, we’ve also started working with recycled grades and other sustainable materials.”
How does MGS maintain such high standards of quality?
Chloe: “Quality is integral to everything we do. Our procedures are backed by our IATF16949 accreditation, which is the latest recognised international quality standard for the automotive sector. We have a strong focus on continuous improvement and rigorous quality control to ensure that we meet and exceed our client’s expectations.”
Sustainability seems to be a key focus for MGS. Can you elaborate on your sustainability initiatives?
Judson: “Sustainability is indeed a core value for us. We focus on making smarter choices and achieving more with less. This includes recycling and reusing plastics, optimising our production processes, and understanding the true carbon footprint of our material choices. Every team member is encouraged to make ethical decisions that positively impact the environment and our stakeholders.”
It’s great to see such a strong commitment to sustainability. Can you tell us about MGS’s involvement in the local community?
Chloe: “We are very active in our local community. Our Managing Director is involved in local regeneration projects, and many of our employees participate in fundraising and community challenges. We also engage with local schools and colleges to inspire young people to consider careers in the plastics industry. It’s about giving back and ensuring that we contribute positively to our community.”
Looking ahead, what are the company’s plans for the next 12 months?
Judson: “We are planning a consolidation year. For the past seven years, we have continuously invested in new injection moulding machines and upgraded our facilities. This year, we aim to consolidate our position and focus on enhancing our in-house tooling capabilities with the recent investment in a new CNC machine. We’re also upgrading our machine monitoring system to InTouch Monitoring, which will further improve our operational efficiency.”
That sounds like a solid plan. Are you planning any events or exhibitions to mark your 50th anniversary?
Mark: “Yes, we are planning several events to celebrate our 50th anniversary this year. We’ll be hosting an industry day and participating in exhibitions such as Southern Manufacturing and Interplas. It’s a significant milestone for us, and we want to celebrate it with our clients, partners, and the community.”
Finally, do you have an official or unofficial company philosophy or mantra?
Judson: “Our company values are centred around our Knowledge, Principles, & Awareness.
“At the core of our business is the culture our people have cultivated through decades of teamwork, innovation, and growth. A dedication to learning and an attitude that would be the envy of any company in any industry.
“We’re proud to mould plastic, and we understand that our people are central to doing it well.”
Mark: “In today’s competitive landscape, to succeed over the long term, you’ve got to be the company that facilitates true partnership. The company, the people, that can always be relied on. That’s who we are.”
Will: “It’s been wonderful speaking with you all. Thank you for sharing insights into MGS Technical Plastics. Your commitment to quality, sustainability, and community engagement is truly commendable, and I look forward to watching your journey continue in the coming years.”
MGS Technical Plastics exemplifies a successful, forward-thinking company that balances innovation, quality, and community engagement. A strong commitment to continuous improvement and sustainability, combined with a solid foundation in technical expertise, positions MGS well for future growth.
As they celebrate their 50th anniversary, MGS Technical Plastics remains a shining example of excellence in the plastic injection moulding industry.
Look out for the next edition of ‘PlastikCity on Tour’ to learn more about our excellent UK-based partners.
There are now well over 260 active partners represented on the PlastikCity site, many of which offer highly specialised products or services to our sector.
During our everyday course of business, we’ll be making a point of visiting as many of these partners as we can and using the time to better understand what they offer the market. We’ll then showcase them through this ongoing series of articles.
Maybe you can benefit from their services!
Read more news from MGS Technical Plastics here.
MGS Technical Plastics
01254 267750
Website
Email