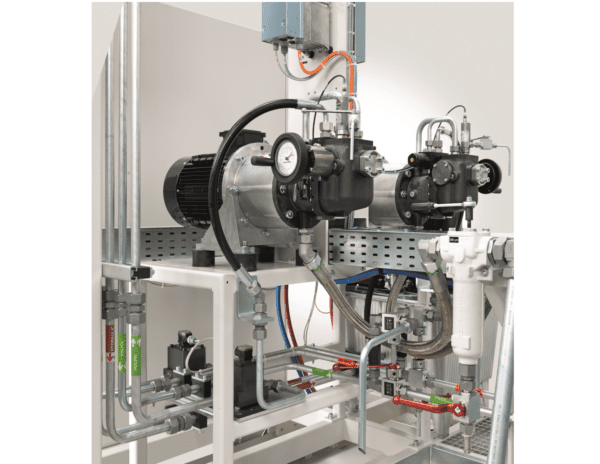
Corrosive or abrasive: New HPP2 PUR Pump from KraussMaffei Can Withstand Anything
Getting your Trinity Audio player ready...
|
Time is money. When PUR systems are expected to react faster and faster, one system component is particularly affected: the pump. Chemistry is becoming more aggressive, and there are often abrasive additives such as foam components. KraussMaffei’s HPP and HPP2 axial piston metering pumps are designed for this and are now available in two new nominal sizes. Customers get the right pump for every chemical.
In reaction technology systems, the pump is the heart of process reliability – and KraussMaffei is the expert cardiologist. The company has been developing its pumps for over ten years. The team led by designer Robert Brunner has now scaled the proven HPP concept to flow rates of 80 and 155 litres/minute (at 1450 rpm) and added useful features. This means that the entire range of PUR requirements can be covered.
If a mixing head is to turn polyol and isocyanate into PUR (polyurethane) in a precise ratio, it needs the worker in the background – the pump, which ensures the necessary throughput in the dosing machine with a pressure of 100 to 200 bar. Chemical versions are in a league of their own within the pump family. Few suppliers dare to tackle this process and even fewer have the necessary expertise.
Construction of the axial piston pump
First of all, you need to understand the structure of an axial piston pump: The drive shaft sets several pistons in motion, which are located in a rotating cylinder housing. This can be infinitely adjusted in angle to the drive axis with the help of a control disk, which changes the flow rate (in cm3 per revolution). The greater the inclination, the higher the displacement, because the length of the cylinder bores is utilised to an increasing extent. Without inclination, the piston stroke is zero. Originally, pumps of this type were designed for the hydraulics of construction machinery, for example, also widely used in reaction technology applications.
Here they face particular challenges, as the pump housing is filled with chemicals that have become increasingly aggressive to enable faster production times. For example, some alkaline components attack the very iron-carbon compounds that ensure the hardness of the steel. Robert Brunner emphasises: “When designing pumps, we therefore have to pay more and more attention to the choice of materials and find solutions here.”
KraussMaffei is the only manufacturer of PUR systems that has been building the pumps for its metering machines itself for many years. Most suppliers rely on standard models, whereby the broad market availability of pumps in this size range is limited. For Jochen Zwiesele (Director of Global Development Reaction Process Machinery), one thing is clear: “The new versions of our HPP pumps close existing gaps.” Previously, they were available with nominal sizes of three to 28 cm3/rev, which corresponded to a flow rate of up to 40 litres/minute. For large-volume applications such as building panels or insulation for refrigerators and district heating pipes, it became necessary to increase the material throughput.
Characteristics of the new PUR pump HPP2
HPP and HPP2 differ from each other in a number of details, although their volumetric efficiency is equally good. Model HPP is fully compatible with the variants available on the market, making it very easy for customers to replace units from other suppliers that are no longer available. It is available with either shaft coupling or magnetic coupling. The HPP2 has a wear-free magnetic coupling as standard.
This works by means of an internal rotor fitted with magnets and positioned in a non-magnetic containment shell. An outer rotor, also equipped with magnets, transmits the desired speed from the motor to the drive shaft. This concept offers a decisive advantage: the housing is closed. With the shaft coupling, on the other hand, the shaft protrudes and good seals are required to prevent leakage, as the PUR components are almost as fluid as water. Seals, in turn, are critical points for wear.
Another feature of the new HPP2 is the spindle, which has been removed from the pump chamber. It is responsible for changing the cylinder inclination via the control disk and thus ensures the optimum operating point for a wide range of applications. Especially with isocyanate, crystals can form due to water absorption, which clogs the thread and makes it difficult to move. By placing this outside the pump chamber (and leaving only a smooth rod there), it is ensured that the handwheel can be moved easily over the long term. In addition, the bearing spacing has been increased, making the bearing stiffer, and temperature sensors and bearing damage monitoring are also available.
KraussMaffei offers a broad portfolio of pumps available at short notice for processing harmless chemical products, water-driven systems and aggressive fluids. The mechanical side is always taken into account. Added dyes such as carbon black or titanium dioxide, for example, can have an abrasive effect. The pump design and materials used must also be adapted to this. In addition to the tried and tested cast housing, the HPP2 in nominal sizes three, six and twelve cm3/rev are also available with a stainless steel housing, which is particularly suitable for epoxy applications.
In-house service with maintenance and testing including certificate for sustainable solutions
The combination of material and process know-how as well as design details makes HPP and HPP2 extremely low-wear, durable and robust and ensures a smooth process. KraussMaffei models are known and appreciated in the market for these properties. Now the next sizes will also accompany their customers.
Although the pumps are optimally adapted to the raw materials to be pumped thanks to several corrosion protection levels and offer a long service life, it is still necessary to clean and refurbish them at certain intervals. KraussMaffei offers an uncomplicated in-house service with maintenance and testing, including certification.
Keeping tried-and-tested system components in good condition also contributes to environmental protection and sustainability. Jens Kompe (Director Sales RPM) emphasises: “Our products are designed for precision and durability. We also offer the ‘turn old into new’ repair concept. Older pumps can even be upgraded to the latest standard by installing higher-quality components and then also receive a test certificate.”
Read more news from KraussMaffei here.
KraussMaffei
+44 (0) 1925 644100
Website
Email