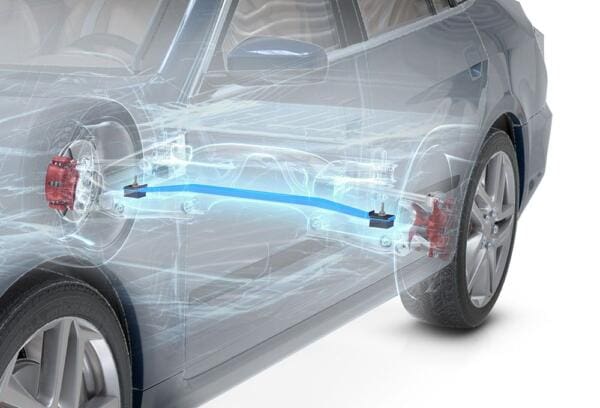
More Efficiency in Lightweight Construction: KraussMaffei Underpins its Leading Pioneering Role at K 2019
Steel is heavy, aluminium consumes a lot of energy during production, and wood weathers. What about a cost-efficient replacement for these materials? Fibre-reinforced plastics (composites) meet all mechanical requirements and are lightweight and weatherproof.
At K 2019 (Hall 15, Booth C24-C27), KraussMaffei will exhibit a wide variety of applications that demonstrate the many possibilities of lightweight construction.
From the idea through series production—Leaf springs made of composites
In the composite leaf spring project, KraussMaffei’s Reaction Process Machinery business unit puts its system expertise on full display. Philipp Zimmermann (Head of BU Composites) and his experts in reaction technology brought it all together to develop a leaf spring for trucks and vans for the customer Hengrui. Manufactured in the HP-RTM process (high-pressure resin transfer moulding), it is 60% lighter than the previous product made of steel. Its strength can be deliberately increased in sections where it is required and the corrosion resistance offers further added value.
A high-pressure metering machine with mixing head and a mould carrier with a pressing force of 800 metric tons are the most important system components in the production of the leaf spring. KraussMaffei is the leader in RTM in all areas, with over 100 machines in the market and the largest pool of process-related expertise. The prototype of the leaf spring was developed in our TechCenter, and our large network of partners was also involved as appropriate: Engenuity developed the component, Huntsman supplied the matrix system made of epoxy resin, Johns Manville supplied the glass fibres, Chomarat created the fibre rovings, Schmidt & Heinzmann manufactured the preforms, Alpex designed the RTM mold and Hufschmied (Bobingen, Germany) took charge of post-mould processing of the component by milling. But Hengrui only has one responsible contact—KraussMaffei, exemplifying the principle of “one face to the customer.”
Pultrusion—New cost-effective applications for construction and automotive industries live at K
When long, thin profiles for windows or rebars for concrete are needed, it is time for pultrusion, the continuous “pulling extrusion” of fibre-reinforced articles. The fibres in pultruded profiles are completely aligned with the direction of load, resulting in finished products that are specially optimised regarding material and weight. “Pultrusion is the most cost-effective way of producing composites, and at the same time, the obstacles for investing in systems and moulds are low,” says Philipp Zimmermann, Head of the BU Composites at KraussMaffei. That is why iPul, the first turnkey complete system which was introduced in 2017, consistently generates high interest, primarily in the construction, wind power and automotive industries. KraussMaffei supports its customers in this process, as well, all the way from component development and prototype creation through series production—which it can even take over for small production quantities.
The iPul system with mould, metering machine and accessories is capable of high production speeds of up to three meters per minute, which is aided by the elaborate design of the mould and the injection box. Close collaboration with material partners Covestro, Huntsman and Evonik make it possible to process highly reactive matrix systems.
Pultrusion has gained more momentum with the takeover of the English provider Pultrex at the beginning of this year. Pultrex has special expertise in the business areas of pullwinding and filament winding and is itself a manufacturer of pultrusion profiles. “The expertise and experience of Pultrex adds to our system expertise. We now provide the complete value chain from a single supplier. At the same time, together, we are pursuing the common goal of advancing standardised systems engineering for pultrusion,” says Zimmermann. At K, new components from the construction and automotive industries optimised regarding weight and costs will be on display.
FiberForm for large-scale production—More than 1 million components per year
A door module carrier in FiberForm technology has been in series production for a long time—and at more than one million parts per year. It is manufactured by forming and back-injecting lightweight but extremely stable fibre-reinforced composites, known as organo sheets. The organo sheet, which is only 0.5 mm thick, ensures the required stiffness with a low dead weight. Injection moulding is responsible for further adapting the component to its function. Compared to a traditional vehicle—that is, one with door module carriers made of steel—the FiberForm technology enables a weight reduction of six kilograms. Intelligent automation solutions and optimised heating technology result in short cycle times of fewer than 60 seconds.
The door module carrier can be manufactured based on fibre fabrics or using organo sheets based on laid tapes, known as UD tapes. UD tapes feature reinforcement fibres of varying widths that are aligned in the same direction. These are made of materials such as glass or carbon and are embedded in a thermoplastic matrix, and can thus be processed into an organo sheet. KraussMaffei’s Extrusion segment is a specialist in manufacturing UD tapes. As a result, this expertise can be combined with the lightweight thermoplastic construction of Injection Molding Machinery to develop completely new material combinations for lightweight construction.
Turnkey systems from a single source
KraussMaffei is the only supplier on the market that has mastered all three technologies of plastics processing (injection moulding technology, reaction technology, extrusion technology), covers the complete process chain for each of them and supplies turnkey systems. The transfer of knowledge across processes makes the topic of lightweight construction so exciting and offers the best solution for each customer. Our global references, especially of real series production, are unparalleled.
KraussMaffei
+44 (0) 1925 644100
Website
Email