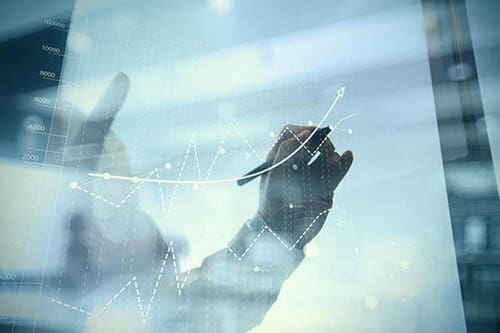
Mergon Delivers Labour Cost Reduction of 60%
Mergon work hand in glove with the design departments of many of their customers. One medical device customer approached them about transferring their in-house product lines from the US to Europe — they weren’t confident the numbers would add up. Mergon thought differently.
Mergon visited the customer site to review the complex processes involved. This included blow moulding, injection moulding, assembly of extruded components, ultra violet welding, leak testing and irradiation.
After many gemba walks, value stream maps, open sharing of information and CAPA review, the team set to analysing the approach needed.
The design and development department forensically reviewed the information gathered at our customer site.
The customer was issued with a proposal that included Class 8 cleanroom blow and injection moulding, 2 cleanroom assembly robots, a packing robot, in-machine leak testing and vision system verification of the finished device with Mergon managing the sterilisation element of the business with a local supplier.
The Mergon proposal was agreed and is now up and running and fully validated at their Irish facility.
Due to the application of lean principles and some clever automation, Mergon make the same product with 60% less labour and faster than the customer achieved in-house.
The reduced labour and cycle time has resulted in the customer making 14% savings in the piece price of the device.
THE RESULTS
The customer’s finished goods inventory is lower and the speed of delivery to their customer is quicker by having local manufacturing. They have also significantly reduced their carbon footprint on the product by transferring the business from the CIS to Europe.
Mergon
+353 44 966 2000
Website
Email