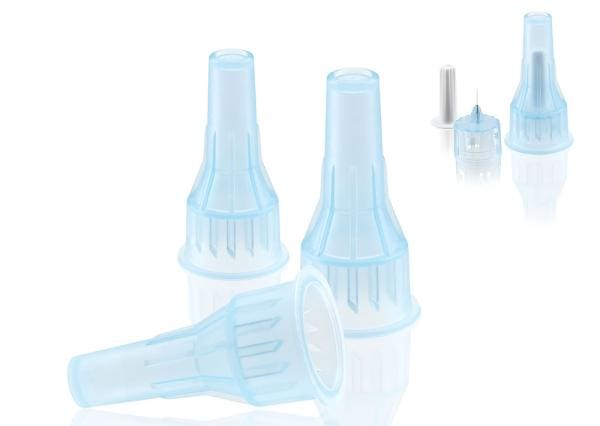
Maximum Efficiency in the Cleanroom: All-Electric KraussMaffei PX 200-1400 Running Live at K
Purity and quality are the keywords for producing sensitive products in medical technology. However, efficiency and cost-efficiency are also increasingly critical. At K 2022 in Düsseldorf (Hall 15, Booth C15/C24-D24), KraussMaffei demonstrates how both can work, using an all-electric PX 200-1400 in cleanroom design as an example. Caps for insulin pens are manufactured with maximum precision under cleanroom conditions, in short cycle times, and with minimum energy and materials.
“Our medical technology customers are in a highly competitive market and face the challenge of increasing their productivity and minimizing costs per produced part,” says Xiaojun Cui, Executive Vice-President of New Machines Business at KraussMaffei. The all-electric PX series in a Medical design is ideal because it combines precision and performance with maximum efficiency and cost-efficiency. The modular concept with an integrated hydraulic unit enables solutions customized to meet customer requirements.
Medical design in cleanrooms
The PX 200-1400 with a clamping force of 2,000 kN at the KraussMaffei trade show booth features a high-gloss machine paint finish. This ensures maximum purity and easy surface cleaning. The automatic central lubrication of the knee lever joints using certified oils and lubricants is in a closed circuit. This, in turn, minimizes maintenance expenses while keeping the production environment impeccably clean. At the same time, it enables cleanroom- and GMP-compliant production.
Short cycle times and lower article costs
The all-electric PX with Performance equipment package ensures short cycle times. With increased power, the process gets a speed boost from a plasticising unit drive. This provides faster plasticizing and, thus, high throughput. The high-performance screw with a unique design for throughput-intensive applications also permits high melt quality with short cycle times. Additionally, the boost in injection speed enables fast and accurate filling of the 96 cavities.
An electric ejector drive with significantly increased performance permits clean demolding at the highest speed. All cavities are always the same, shot after shot. At the KraussMaffei trade show booth, each shot yields 96 caps for polypropylene in a cycle time of 6 seconds and a shot weight of 105 g.
The APCplus machine function provides additional optimization of manufacturing costs. The intelligent machine function compensates reliably for external influences on the end product quality in the injection molding process while maintaining precise tolerances for intervention. The result is consistently high component quality because APCplus uses a predefined process window to readjust parameters, which is otherwise a manual process. This makes it possible to reduce the scrap to a minimum. This, in turn, optimizes material consumption and lowers costs per component. In addition, the APCplus function also enables seamless documentation of the material quality, which makes it possible to recognize significant fluctuations at an early stage.
Best energy efficiency
Soaring energy prices are making energy-efficient production more critical all the time. The all-electric KraussMaffei PX 200-1400 features equipment that makes it a perfect fit for saving energy. In addition to the servo design of the hydraulic unit and the recuperation system for recovering brake energy, the PX features the proven Eco-Pac insulating strips on the injection unit. They stabilize the temperature profile and increase process stability. The heating time is reduced by up to 30 percent.
Even more significant energy savings are possible with the Orca mold cooling system from Jurke Engineering. The system is fully integrated into the MC6 machine control system. Unlike a conventional water distributor, the system uses ultrasound to measure the flow velocity and quantity. This takes place from the outside and without making contact with the medium. As a result, the Orca distributor block does not have cross-section narrowing, meaning fewer pressure losses. Energy efficiency is improved, the cycle time drops, and the quantity produced per hour is boosted.
Additional partners for the trade show exhibit are Männer (molds), Max Petek (laminar flow boxes), ExxonMobil (PP material), Gammaflux (hot runner controllers), and Getcha (grinders).
PX 200: Part of the circular economy circuit live at K
The PX 200 is part of a complete circular economy circuit at the KraussMaffei trade show booth. After being shredded, the manufactured insulin pen caps serve as the basis for an upcycling process with a ZE 28 BluePower twin-screw extruder. Here, various additives, such as bonding agent and liquid dye, are added, blended, and homogenized. The recompound of this yield reaches the following injection molding machine, the new powerMolding 1300-11900 with a clamping force of 13,000 kN. This machine turns it into an automotive front-end carrier made of 100 percent recycled material. The complete material cycle also integrates many new digital solutions with which maximum savings can be achieved for both energy consumption and the CO2 footprint.
KraussMaffei at K 2022, Hall 15, Booth C15/C24-D24
Read more news from KraussMaffei here.
KraussMaffei
+44 (0) 1925 644100
Website
Email