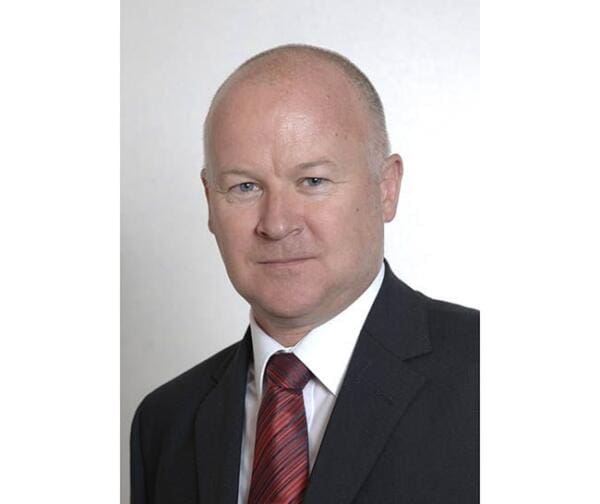
HotSeat – Richard Brown, Managing Director at RJG Technologies Ltd
RJG Technologies is an independent company offering injection moulding process support, training, and consultancy services. They have engineers operating throughout the world, with established customers in Europe, Asia and North America. The UK team is headed by Managing Director, Richard Brown, who has been with the company for over five years. He is the next PlastikCity Partner to face the HotSeat…
What trends do you think will shape the future of UK plastics? How will RJG Respond?
The UK plastics industry currently suffers from a severe skills shortage, and to stay competitive, the industry needs to have access to skilled workers. We could be facing a post-Brexit skills crisis if departing the EU results in fewer plastic engineers coming to the UK.
This issue comes mainly from a general lack of training and apprenticeships, changes in technology and in the skills needed.
Enlightened companies are addressing the skills gap by strengthening their training plans, setting up training academies and offering apprenticeships. However, this is erratic and many companies are still seeking out people with proven track records which results in a ‘war of talent’ between companies.
We are witnessing years of neglect by government, closing down training centres and technical colleges and not recognising the value of apprenticeships. What we are currently seeing with the introduction of the apprenticeship levy, is an attempt to reverse the decline but it is a policy not well thought out.
There is no quick fix to this but it is imperative that the industry builds for the future generation of talent by investing in training and offering more apprenticeships.
We can look to Europe to see how Germany approaches this where they have a vocational training programme available which is there as an alternative to higher education. The UK government are attempting to replicate this with the introduction of T Level courses, which will be on par with A levels and will, it is envisaged, provide young people with a choice between technical and academic education post-16. However, the German apprenticeship scheme successes will be hard to replicate in the UK as there is no established infrastructure to support this T level initiative where a three month placement in industry is required.
The clock is ticking and with retirement looming for many long term staff, companies are finding it harder to find people with the right skills due to decades of underinvestment in training.
At RJG we have developed a full portfolio of courses from Fundamentals to High Performance moulding with The Institute of Materials, Minerals and Mining (IOM3) endorsing these for Continuous Professional Development (CPD). We have developed an apprenticeship for a Science Manufacturing Technician in Polymer Processing and RJG are on the Register of Apprenticeship providers to deliver this. We are also a PAAVQ/SET centre and can provide a Level 3 Diploma in Polymer Processing. With these initiatives we are well placed to meet the needs of our industry.
I fear though, that with the various cut backs over the years, our government is operating on a wing and a prayer with respect to Technical training and I am not confident about the long-term future unless there is less rhetoric and more action.
How has RJG developed during your tenure?
Initially I joined the business in 2014 when it was G&A Technology and after two years they were acquired by RJG Inc. The two companies were polar opposites, the former monocratic the latter with a people centric culture. It has been challenging but very satisfying leading the changes to develop a team culture to achieve the goals of the business. I now lead a great team who have a shared vision – ‘Always looking to develop and improve to ensure we are the best we can be, as people, as a team and as a company’.
What do you credit as the key to your success?
I started my career as an apprentice toolmaker with Tube Investments who had a comprehensive structured training programme. I spent the first year at an EITB training facility and was taught the basic skills after which I toured the various departments of the business to learn my trade. I was fortunate to have good mentors, both in the workplace and at the Technical and Polytechnic Colleges I attended who provided advice as to how to gain experience post apprenticeship. However, the overriding support to my success has been the support of my wife which she has provided throughout my career as I have moved into different roles in different counties and countries.
What has been the greatest challenge in your career?
There has been many through my career as moving companies and countries all have their own different aspects. There are three that come to mind. Firstly, leaving an established role as a Technical Director to set up a Design Consultancy and working with a great team to make it a success. Secondly, setting up a moulding facility on a brown field site in Eastern Europe, working with local government and suppliers. Finally, right now as the skills shortage hugely impacts the industry, RJG have to remain at the forefront of delivering the training the industry needs from apprenticeships to upskilling the current workforce.
What advice do you wish you’d had on entering the industry and does that differ from the advice you would give an apprentice joining now?
During my formative years in the industry I was advised to gain as much experience and exposure as I could. I was encouraged and told it was important to gain my qualifications, absorb the teaching provided, and listen to the opinions and advice given to be able to make informed decisions. This advice I believe has enabled me to become the person I am today.
I do not believe this has changed but I would advise anyone looking for an apprenticeship is to ensure that there is a complete infrastructure in place for them to be successful with a defined career path. (see BPF career zone http://www.bpf.co.uk/polymer-zone/career-zone/career-pathways.aspx.)
I am in a unique role now where I see the development of apprentices we have trained and also the design students that have been finalists of the Design Innovation in Plastics student competition for which I am the chair of judges. We have a lot of talent in the UK that we need to nurture and encourage.
What hidden talents do you have?
In the long distant past I learnt to play the bagpipes.
RJG Technologies Ltd
+44 (0) 1733 232211
Website
Email