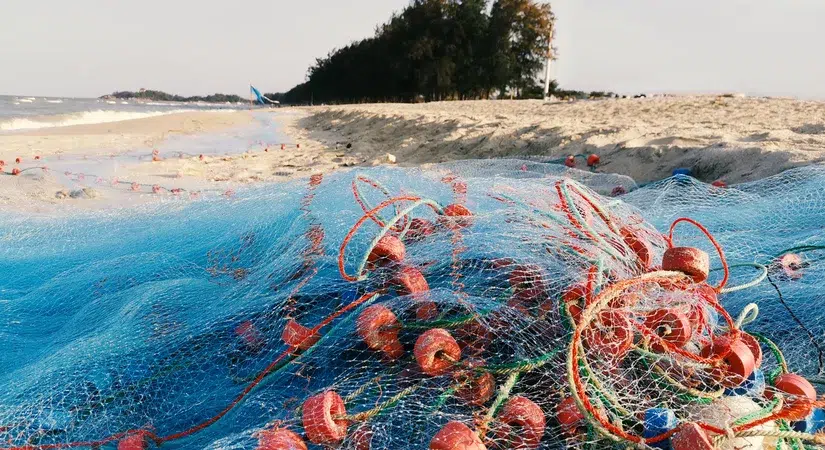
From the Sea into the Tunnel: KraussMaffei Customer Oldroyd Uses 100% Sea Plastics for its Products
What do a tunnel and hiking boots have in common? Both have a membrane that prevents the ingress of rain. In the case of the tunnel, the Norwegian company Oldroyd is an expert for the membrane and its injection-moulded fixing product. It uses CX machines from KraussMaffei and 100% sea plastics.
Tunnels are an everyday phenomenon in Scandinavia because they are used to get around the many fjords. Norway alone has over 900 tunnels, and the world’s longest road tunnel is also located there. The enclosures for the traffic are more complex than one might think because a sophisticated membrane system lies behind the pipes visible to the driver. This system prevents water from penetrating the soil and causing damage to the concrete.
Oldroyd is the top dog in the area of waterproofing against rain and holds over 90% of the market share in Nordic countries. The key to success lies in the innovative strength of the family business in Stathelle (around 160 kilometres southwest of Oslo). Originally concentrating on film extrusion, founder John Oldroyd Cheetham also accessed the injection moulding technology with the help of KraussMaffei and now successfully operates three hydraulic CX 160-750 with a clamping force of 1600 kN.
So-called spacers, curved products with a grid structure, which create a distance between rock and membrane, are produced on these machines in a cycle time of roughly 15 seconds. They weigh approximately 150 grams, whereby there are around 20 different models, varying in diameter and height.
100% sea plastics
300,000 to 400,000 of the spacers are required for one tunnel alone. For these quantities, it pays off ecologically to use recycled materials. Oldroyd uses 100% sea plastics, consisting of roughly half PP and half PE. The remnants of broken fishing nets and plastic ropes are collected on the coast of Norway by specialist companies and crushed, washed, and granulated. The subtle fish scent does not need to be removed for the tunnel construction.
The APCplus machine feature is very helpful for changing material compositions and resulting viscosity fluctuations. It ensures a constant shot weight by adapting the switchover point and the pressure level from shot to shot.
Safe “ghost shifts” at the weekend
Efficient automation is required in order to be able to produce plastic products competitively in Europe. All Oldroyd machines are therefore equipped with oversized LRX robots from KraussMaffei. With their very long vertical axle, these large quantities of manufactured products can be stacked up – starting with a ground-level pallet up to a height of two meters. In the case of the tunnel spacers, this volume covers the production of one (unmanned) weekend exactly.
2-component project with TPE
A new CX with two-component equipment will soon go into operation at Oldroyd because John Cheetham has once again made a development that will change tunnel construction: a 2-component platen, called RoadStar, which is secured on the steel rods that connect the concrete wall and the rock layer. Up to now, these platens were made of metal and corroded accordingly, which is why maintenance is required and a replacement after roughly 50 years. Whereas the RoadStars were estimated to have a service life of 120 years in special ageing tests. This alone saves a lot of resources. The RoadStar was already tested by Oldroyd customers and was also widely accepted because the integrated TPE layer has a sealing effect, while the other side (made of PE) is impact-resistant. Success on the market and the correspondingly high numbers of units will mean more 2-component machines will make their way north from Munich.
Read more news from KraussMaffei here.
KraussMaffei
+44 (0) 1925 644100
Website
Email