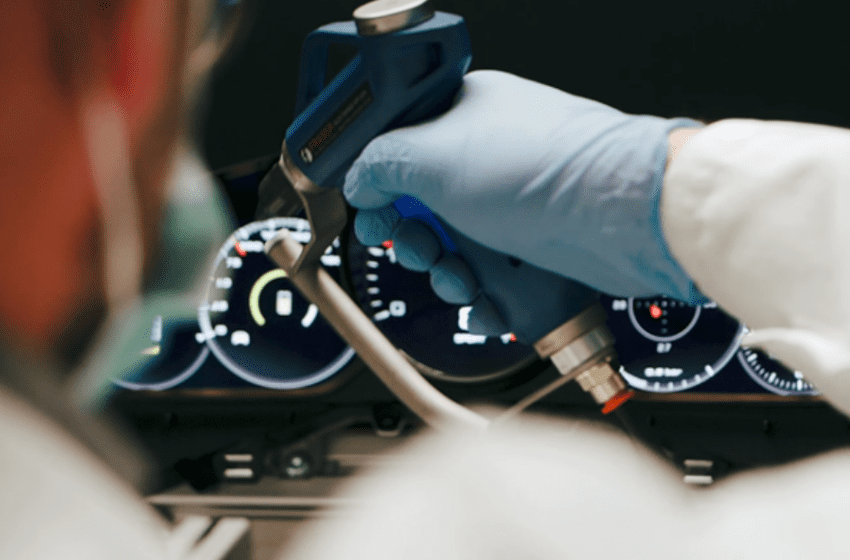
Seeing Things Clearly: How an Anti-Static Solution put Panel Graphic in Pole Position
Getting your Trinity Audio player ready...
|
Norwich-based Panel Graphic is a multi-award-winning manufacturer of high-quality optical plastic parts. It has developed a unique range of surface coatings for plastic that are used to create parts for everything from luxury cars to life-saving fire detector systems and medical equipment. Steve Earl MBE and his team identified a problem with static in its production and called in Fraser Anti-Static Techniques to help.
The family business is run by Steve Earl MBE, managing director and owner. Steve was awarded an MBE for services during Covid where he pivoted the factory’s output to help meet the demand for essential protective equipment, producing 350,000 visors.
Steve and his team identified a problem with static in its production and called in Fraser Anti-Static Techniques to help.
Optical plastics for the fast lane
The plastic parts created are largely used for display screens of all types and optimised for different conditions, from bright sun to darker environments. Favoured by high end manufacturers including McClaren and Rolls Royce, the screens are of the highest quality. Panel Graphic’s reputation is its key selling point.
Items are machined, printed, or coated with special finishes to make them abrasion resistant or give them a surface that removes reflection. This allows the customer or consumer of a product to read an information display more clearly, even in changing light conditions, vital on a McLaren racing car, for example. These plastic-based processes mean static is a key issue during production.
Static can cause a series of problems, from the immediate (team members experiencing a static electric shock) to the longer term (delays in the production process, high rejection rates and a poorer quality product due to contamination with particulate matter). Before turning to Fraser Anti-Static Techniques around 10 years ago, the company was using an anti-static solution that was not performing.
Managing Director, Steve Earl explains: “Every part we produce needs to be perfect. We produce materials for some of the highest performing products available and our standards are high to match. As we are working with plastic, static is a key focus for us. Every one of our machines has anti-static equipment. Prior to working with Fraser, we had sourced a cheaper import which, while low cost, regularly broke and did not perform well. We turned to Fraser who recommended a series of products to us, and we’ve not looked back. That was 10 years ago.”
A collaborative solution
Kevin Brown, Head of Sales UK, Fraser Anti-Static Techniques, worked with Steve to develop the static solution. He began by visiting the site and looking at the whole process from start to finish.
Kevin said: “We’re delighted with the results we’ve been able to achieve for Steve and his team at Panel Graphic. It is crucial we understand every part of the production process so that we know where the Fraser products can be the most effective. Many businesses are aware that static is problem but don’t know how to get rid of it. Often there is a misconception that if you get rid of static once in the production process then it’s gone for good, but this isn’t the case. A very small amount of static charge can have a very big impact and dealing with that can make a massive difference, ultimately reducing rejection rates and waste. This is hugely significant both for profit margins and environmentally.”
The Fraser equipment has delivered multiple benefits for Panel Graphic including:
Improving production efficiency: Using anti-static air guns to clean products rather than standard air guns means that the products are cleaned of any contaminants within seconds on the first attempt rather than a team member having to repeatedly apply air to remove further particulates. The cleaning process itself is a static-generative process so using a standard air gun without anti-static technology can make the problem worse in the short term and cost significant time.
Minimising rejection rates: The use of anti-static technology dramatically reduced rejection rates.
Steve explains: “If our internal fall out percentage ever increases, the first thing we normally check is that the anti-static equipment has been used effectively. This demonstrates how much difference using anti-static technology makes to the end quality of the product.”
Enhancing product quality.
The Fraser products used by Panel Graphic are so effective that they ultimately enhance the end quality of the product, making the good even better.
The impact on both rejection rates and the associated plastic waste mean that the equipment has paid for itself many times over.
Steve explains, “What I like about Fraser is that the products are clearly very well made. There is a lot of anti-static equipment that is cheaper but does not have the reliability or performance. Right down to the comfort for our team members in using them, which is important given how key the equipment is to the production process.”
“I would not recommend any other manufacturer for anti-static control. The return on investment comes through productivity but also in product quality which for us, supplying the customers we do, is vital. We were buying guns for a lower cost and saw an instant improvement when we tried the Fraser products.
“There is no better way of seeing these benefits than by trying the equipment and seeing what it is capable of. It has had a profound impact on everything we do. Our team members pick up an anti-static product every 10-15 minutes. It is an integral part of our process and allows us to maintain our reputation for quality products.”
Panel Graphic is still using original units, many years after installation, to maintain competitive advantage by delivering best-possible quality, minimising waste and maximising efficiency.
Read more on Fraser Anti-Static Techniques here.