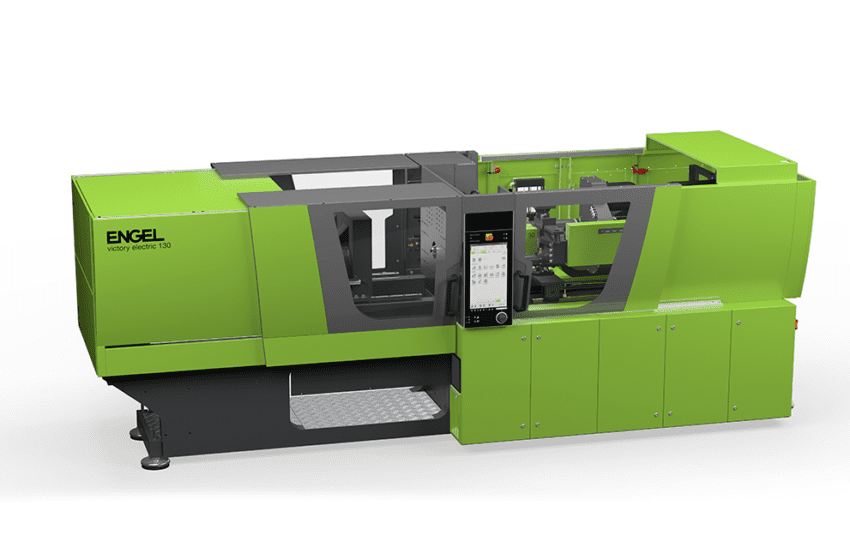
ENGEL Announces the Expansion of its Victory Series
Getting your Trinity Audio player ready...
|
ENGEL is expanding its renowned tie-bar-less victory injection moulding machine series with the integration of the previous e-motion TL, now introduced as the victory electric. This innovative addition combines the strengths of tie-bar-less technology with the advanced features of servo-electric drives, setting new standards in production technology.
By incorporating the successful e-motion TL into the victory series under the name victory electric, ENGEL has restructured its portfolio of tie-bar-less injection moulding machines, offering three distinct categories within a single series: electric, hybrid, and hydraulic.
The machine has been upgraded with state-of-the-art drive components for improved energy efficiency. The redesigned injection units deliver faster injection speeds and enhanced user-friendliness. Components are now more accessible and easier to replace, simplifying maintenance tasks such as the servicing of the plasticising cylinder. These improvements result in higher performance, energy savings, and increased machine availability.
A further innovation of the victory electric is the integration of hydraulics for clamping forces starting at 80 tonnes. This meets market demands for a variety of tools requiring hydraulic support. Additionally, this solution is significantly more cost-efficient than externally supplied hydraulics, while maintaining the machine’s compact footprint.
The victory electric is available in clamping forces ranging from 30 to 130 tonnes, designed to meet the needs of industries requiring high flexibility, exceptional precision, and short cycle times. Key application areas include sectors demanding large quantities of high-precision parts in short cycles, such as medical technology, the automotive and electronics industries, as well as technical moulding. With this machine, ENGEL aims to further strengthen its market leadership in these sectors.
The victory electric delivers precision in two stages. First, its electric injection units ensure highly accurate control of the injection moulding process, shot by shot. This results in significantly improved part quality and exceptionally low scrap rates – a major advantage in cost-intensive production environments. Another benefit of the electric drive system is its short response times. This enables very short cycle times while maintaining consistently high part quality. In high-volume production, where every second counts, this provides a distinct competitive advantage.
Even distribution of clamping force across all cavities is crucial for the production of high-quality components in high-cavity moulds, representing the second stage of maximum precision. Part by part, within each shot. Furthermore, the excellent platen parallelism of tie-bar-less injection moulding machines is a key feature for protecting moulds, which translates into reduced maintenance costs.
The large, unobstructed mould area of the tie-bar-less design in the victory electric also simplifies mould changes and accelerates maintenance operations. This increases overall uptime and significantly reduces production costs. It also enables the use of very large and complex moulds without requiring an alternative tie-bar machine with significantly higher clamping force. The compact design and small footprint of the machine make it particularly advantageous for facilities with limited space or cleanroom environments.
Since the victory electric is equipped as standard with an encapsulated toggle lever, the risk of oil leaks and contamination is significantly reduced. The absence of tie bars minimises airflow turbulence, which can dislodge dust and debris in the mould area. Both features are especially important in clean production environments, such as in medical technology. With the specially developed optional cleanroom package, qualifying the machine for use in cleanrooms up to ISO Class 7, ENGEL also sets benchmarks in cleanliness. The enclosed components and low-emission operation make the victory electric the ideal choice for industries requiring the highest cleanliness standards.
The expansion of the victory series through the integration of the victory electric reflects ENGEL’s commitment to offering solutions for every injection moulder – with technological advancements aimed at increasing production efficiency and reducing operating costs. Customers benefit from a future-proof investment that guarantees superior product quality and environmental standards, ensuring competitiveness in demanding markets.
Read more news about ENGEL here.
ENGEL
+44 (0)1926 335000
Email
Website