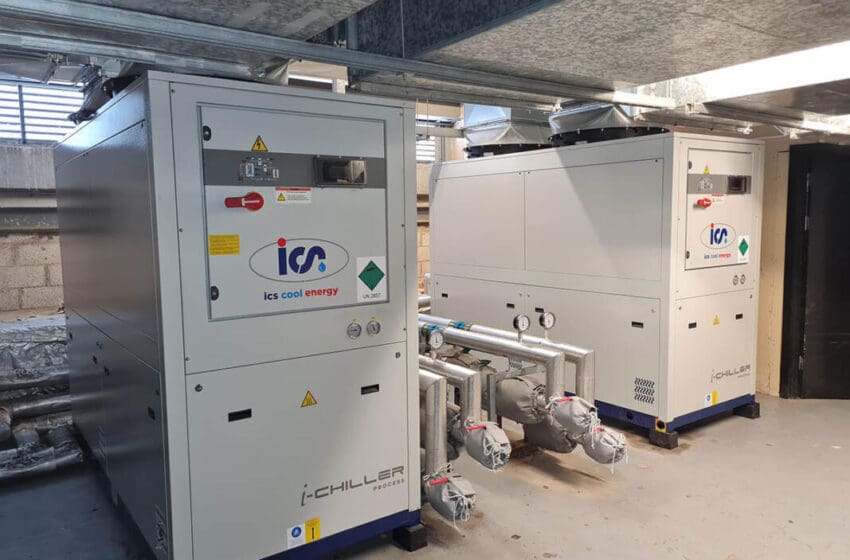
ICS Cool Energy Upgrade Critical Cooling Systems for a Hospital in Scotland
Getting your Trinity Audio player ready...
|
Reliable temperature control systems are critical to the smooth operation of any healthcare facility, ensuring that essential medical equipment, sensitive medications, and hospital environments are maintained at precise temperatures. In operating theatres, laboratories, and storage areas, temperature control is essential to prevent equipment failure, ensure patient comfort, and safeguard the quality of critical supplies like vaccines or pharmaceuticals.
For these reasons, hospitals rely on efficient cooling systems that deliver consistent performance even under challenging conditions.
The Challenge:
In a hospital in Scotland, the outdated cooling infrastructure serving the operating theatres was posing a risk to ongoing operations. The hospital urgently needed a reliable and efficient replacement system to avoid potential issues.
The hospital specified a cooling capacity requirement of 80kW for chillers located indoors in a 30℃ ambient temperature. However, the plant room’s location on the upper floors of the building created logistical challenges for equipment dismantling, transport and installation of the new one.
The Solution:
Tasked with the challenge, ICS Cool Energy developed a plan to remove the old equipment and install new chiller systems in the hospital’s covered plant room. Due to limited access and the challenge of transporting large equipment to the upper floors, several site visits were conducted to assess the layout, identify potential obstacles, and establish an effective work process.
To meet the hospital’s cooling requirements, ICS Cool Energy selected two i-Chiller 80kW units. The selected chillers were transferred from ICS Cool Energy’s central storage in Totton to their workshop in Bradford, where the units were de-gassed, disassembled, and flat-packed onto pallets to facilitate easier transport. The flat-packed components were then shipped to the hospital’s loading area, from where they were transferred manually to the fourth-floor chiller plant room via internal lifts. A manual lift and shift team then laid out the components for on-site reassembly by ICS Cool Energy engineers.
After reassembly, the system was recharged with refrigerant, tested and commissioned following the completion of pipefitting, fluid filling, electrical supplies, and ducting.
ICS Cool Energy also issued Waste Transfer Notes for the redundant equipment, refrigerant and oil.
Al Sorley, sales engineer at ICS Cool Energy: “One of the primary challenges was transporting and installing the new chillers. Due to the restricted access to the fourth-floor plant room, we had to disassemble the chillers for transport and then reassemble them on-site. This complex logistical process required precise planning and coordination to ensure minimal disruption to hospital operations, especially in critical areas like the operating theatre.”
The Result:
ICS Cool Energy demonstrated its expertise in providing tailored solutions by selecting and installing a system that met the hospital’s specific cooling requirements. By overcoming the complex logistics of disassembling, transporting, and reassembling the chillers in a restricted-access area, ICS Cool Energy minimised disruption and completed the installation efficiently. The hospital now benefits from a reliable, energy-efficient cooling system, ensuring long-term operational stability and reduced risk of equipment failure, enhancing patient care and safety.
For more information on ICS Cool Energy’s complete process temperature control solutions, please visit www.icscoolenergy.com/.
Read more news on ICS Cool Energy here.
ICS Cool Energy
+44 (0) 23 8052 7300
Website
Email