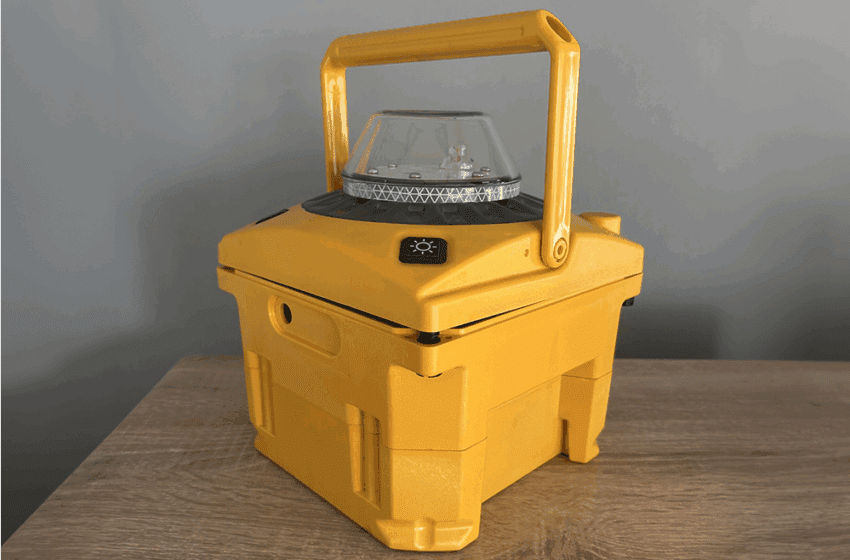
BEC Group Blog // Why Use Injection Moulding for Enclosures & Housings?
Getting your Trinity Audio player ready...
|
When creating a product for the market with important components, you want to make sure it’s functional, attractive, and well-protected. That’s where enclosures and housings come in. These essential components are designed to protect your product’s internal parts from damage, dust, moisture, and other environmental intrusions, as well as knocks, drops, and other shock or vibration. So, how do you choose the best manufacturing process for your enclosures and housings? The answer is quite simple: injection moulding. In this blog, BEC Group explores why injection moulding is the best choice for creating enclosures and housings, highlighting its versatility, efficiency, and cost-effectiveness.
Enclosures and Housings: The Protectors of Your Product
Enclosures and housings protect your product, holding components together. They’re the first line of defence against the wear and tear of daily use.
Before we move on, here’s a quick breakdown of each and what they do:
- Enclosures are the outer shells that surround and protect electronic devices like GPS devices, radios, and medical equipment. They keep the delicate internal components safe and provide a sleek, attractive, and user-friendly interface.
- Housings are protective casings for mechanical parts like gears, motors, and pumps. They shield these components from contaminants while allowing for proper ventilation and easy maintenance access.
Now let’s explain how and why injection moulding is the best way of creating them:
Why Injection Moulding is a Winner
Plastic injection moulding is one of the most common and cheapest ways of producing 3D plastic parts, but what makes it the go-to choice for creating enclosures and housings?
It comes down to a combination of versatility, efficiency, and cost-effectiveness:
- Design freedom: Injection moulding gives you incredible design flexibility, allowing you to create complex shapes, fine details, and precisely tuned dimensions.
- Speed and volume: Once you have a mould tool designed and made for your part, you can churn out hundreds or even thousands of identical parts in a matter of hours, making it perfect for mass production.
- Material options: Injection moulding is compatible with a wide range of thermoplastics, each with its unique properties, so you can choose the best material for your project. Whether you want a flame retardant, water-resistant, or recycled material, we can help you do this.
- Cost-effectiveness: While the initial cost of creating a mould tool might seem steep, injection moulding is incredibly cost-effective in the long run, with the cost per part dropping dramatically as your production volume increases.
At BEC Group, we understand the important role that enclosures and housings play in your product’s success.
That’s why we offer a full range of plastic injection moulding services – from design to tooling and production – to help you create the perfect protective solutions for your products.
Best Practices for Designing Enclosures and Housings
To get the most out of plastic moulding for your enclosures and housings, keep these best practices in mind:
- Consider your product’s specific requirements: Think about the environmental factors your product will be exposed to, as well as any necessary features like ventilation, access points, or mounting options.
- Optimise for manufacturability: Work with your tooling and injection moulding partner to design enclosures and housings that are suitable for injection moulding, with uniform wall thicknesses, proper draft angles, and minimal undercuts.
- Choose the right material: Select a thermoplastic that offers the right combination of properties for your application, such as strength, durability, heat resistance, or electrical insulation.
- Plan for assembly: Design your enclosures and housings with assembly in mind, incorporating features like snap fits, threaded inserts, or locating pins to streamline the production process.
BEC Group can help you implement each of these best practices, ensuring that your enclosures and housings are optimised for both form and function.
Click here to read the latest news from BEC Group.
BEC Group
+44 (0)1425 613131
Website
Email