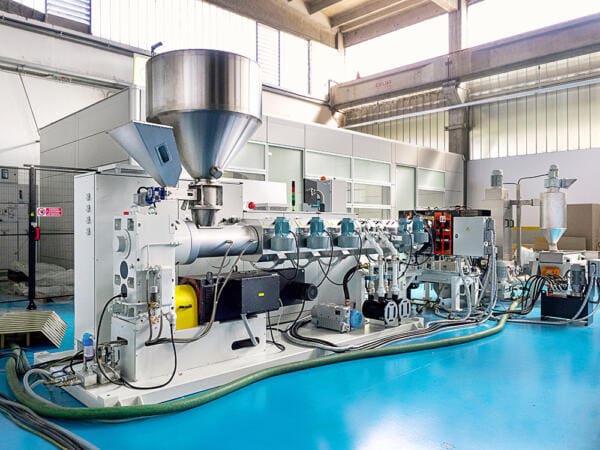
Bausano In-House Production Facility Develops Regranulation Recycling Technology
Bausano, in partnership with Intelicare in the UK & Ireland, is a family company designing and producing innovative extrusion and recycling lines for plastics processing. For more than 70 years, Bausano have continually pursued new technology and put the customer at the heart of everything they do.
Bausano have developed two recycling and pelletising systems with optimised L/D ratio, and filtering ahead of vacuum degassing, especially suited to waste plastics such as highly contaminated and heavily printed recycling and pelletising:
MD Series for PVC Regranulation
Bausano designs and builds a plastic recycling extruder for PVC plastic material. As one of the most widely used polymers in the plastics industry, it also means that it is one of the most recycled. Bausano’s MD Twin Screw Extruders are designed especially for PVC regranulation.
EGO R Series
The Bausano E-GO R series single screw extrusion and pelletising system is a specialised and reliable system, suitable for recycling and re-pelletising of polyolefins. It combines function of plasticisation and pelletising to one step and is ideal for crushed regrinds or flakes including PE, HDPE, LDPE and PP.
In-House development increases quality; reduces lead times and cost
Bausano’s extrusion lines are unique because all critical components are designed and manufactured entirely in-house. This includes screws, barrels, gearboxes for twin-screw extruders, die-heads, and downstream equipment. With complete control over every aspect of the extrusion line, Bausano can create bespoke lines to meet the exact specifications of our customers.
To facilitate in-house production, the Bausano factory houses multiple state of the art facilities designed to make development a smooth process. The Design Department is where individual projects take shape including the design of screws and other vital components. In the Production Department 100% of the components, including the screw, barrel, and multi-drive system are manufactured from scratch before the extrusion lines begin to take shape in the Assembly Room.
The jewel in the crown at Bausano is the Test Room where customer’s extrusion lines are set up and carefully tested prior to despatch. Customers are able to view their lines being demonstrated if they wish to visit the Bausano factory. This room also houses the laboratory where customer material samples are analysed with dedicated laboratory equipment and an expert team. This is a vital resource available to Bausano customers to help ensure customers get the exact equipment they need for their project.
Bausano and Intelicare: supporting UK manufacturing
Bausano and Intelicare have a longstanding, exclusive partnership in the UK and Ireland, meaning they can also offer project management from any point within the project’s progress; rapid technical support and training; quick delivery of spare parts and aftermarket sales; regular servicing; and complete commissioning.
Bausano will be present at Plast 2023 (Hall 13, stand 41/42) and InterPlas 2023 (Hall 4, Stand J9) with exhibitions that perfectly interpret its three distinctive values: tradition, innovation and respect for the environment, for a journey that celebrates sustainable extrusion in all its forms.
Read more from Bausano here.