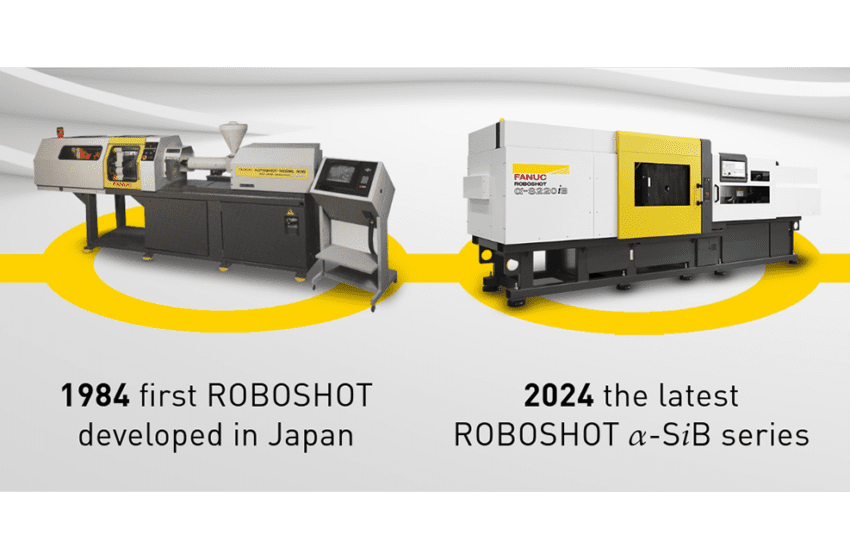
FANUC Celebrates 40 Years of Roboshot Injection Moulding Efficiency
Getting your Trinity Audio player ready...
|
FANUC is marking the 40th anniversary of its high-performance all-electric ROBOSHOT injection moulding machine celebrating its sustainability, reliability and low total cost of ownership (TCO) credentials. First developed in Japan in 1984, the FANUC ROBOSHOT is widely used by plastics manufacturers around the world to automate their injection moulding processes.
FANCU’s ROBOSHOT machine has evolved over the past four decades to meet the ever-changing needs of end-users, with today’s models boasting AI capabilities as standard. The machine is super energy efficient, with its advanced servo technology and intelligent energy recovery systems also mean the ROBOSHOT consumes up to 70% less energy than its hydraulic counterparts, and 5-10% less than other electric machines.
AI-enabled features showcased at FAKUMA
At the recent FAKUMA 2024 exhibition in Germany (Oct 15-19), FANUC showcased the versatility of the ROBOSHOT range with a series of live demonstrations. These included:
- A fully automated production cell processing sustainable biopolymers, longitudinally-mounted on an additional linear axis to minimise footprint. Comprising of a ROBOSHOT a-S150iB with a clamping force of 150 tonnes and an LR-10iA compact 6-axis robot, it highlighted how moulding shops can significantly increase their output.
- A showcase of the AI functions of the latest A-iB series ROBOSHOT. The injection unit includes AI metering that uses torque (rather than speed) control to compensate for changes in material viscosity, such as drying conditions and variations in regrind. In addition, AI mould and ejector protection avoids mould damage and costly repairs/downtime should an event occur during the opening and closing cycle. It even indicates when greasing is necessary or if the mould is showing signs of wear. The same technology also protects the ejector’s forward and reverse movement.
- The ROBOSHOT a-S100iB, presented together with the SEPRO Success 11 robot. Demonstrating the flexibility and versatility of FANUC’s injection moulding solutions, it enables precise and fast handling of plastic parts with seamless integration of third-party robots.
Industry-beating TCO
Long renowned for having the industry’s lowest TCO, all ROBOSHOT machines feature a power consumption screen as standard. This includes an energy analysis page to identify where energy consumption takes place during the cycle, to aid optimisation. Further features contributing to low TCO include high reliability and machine uptime, along with low wear, simple mechanisms with fewer components, and high spare part availability. All of this adds up to an average cost of just €555 a year (parts and service) to run a ROBOSHOT machine.
“It’s clear to see why the ROBOSHOT has remained so popular with injection moulding customers for four decades,” says Andy Armstrong, FANUC UK’s Vice Managing Director and Head of ROBOSHOT European Sales. “Superior precision and extremely short cycles mean it is capable of producing large quantities of consistently high-quality parts, with unbeatably low energy consumption. Its reliability and energy efficiency are enhanced with the latest AI technology, ensuring the ROBOSHOT can continue to help manufacturers produce the highest quality goods at the lowest total cost of ownership.”
Read more news from FANUC here.
FANUC
+44 (0) 24 7605 3000
Website
Email