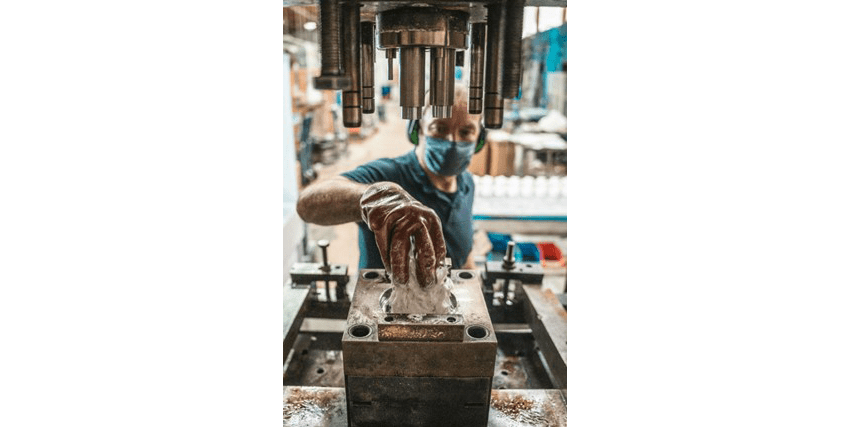
Fairgrieve Compression Moulding Blog // Compression Moulding: A Time-Tested Process Meeting Modern Manufacturing Demands
Getting your Trinity Audio player ready...
|
While contemporary plastic moulding processes dominate the conversation, compression moulding remains a critical and often underappreciated method. Its unique benefits make it the process of choice for specific applications where other techniques fall short. In this blog, Fairgrieves talks about why this moulding technique is ideal for industries needing high-performance materials in challenging environments. It offers unmatched durability, lower tooling costs, and versatility.
What is Compression Moulding?
Compression moulding involves placing a polymer material into a mould cavity. Pressure and heat are applied, causing the material to flow and take the shape of the mould. The component is then cured and ejected, often requiring minimal post-processing. This technique can process both thermoplastic and thermosetting materials, giving manufacturers a wide range of options depending on the application’s demands.
Why Opt for Compression Moulding?
Compression moulding’s primary advantages lie in its ability to handle complex, large components, often with exceptional material properties. When compared to other moulding methods, compression moulding stands out for its:
- Material Versatility: Compression moulding is especially practical for thermosetting materials like phenolic resins and silicones. These materials offer high mechanical strength, resistance to extreme heat, and outstanding electrical insulating properties, which are critical in the automotive, electrical, and aerospace industries.
- Durability and Strength: The pressure applied during compression moulding ensures that the final product is dense and uniform. This results in parts that can withstand significant stress and perform reliably under harsh conditions, such as high temperatures and pressures or corrosive environments.
- Cost Efficiency for Complex or Low-Volume Products: While compression moulding may have slower cycle times compared to other methods, it offers lower tooling costs, making it a cost-effective option for prototype production and medium to low-volume production runs, especially when high precision or intricate part designs are required, and high-speed manufacturing isn’t required.
- Produced with minimal waste: Compression moulding is highly efficient when it comes to material usage, as only the exact amount of material needed is placed into the mould, minimising excess.
- Integration of Inserts and Reinforcements: One of the unique advantages of compression moulding is the ability to embed other materials, such as metal or composites, directly into the moulded part during manufacturing. This allows for the creation of components that combine the properties of both the plastic and the insert, enhancing the functionality and durability of the final product. For instance, metal fasteners or reinforcing plates can be moulded directly into automotive or electrical parts, offering added strength or conductivity. This process improves performance and reduces the need for additional post-production assembly, making compression moulding a highly efficient and versatile manufacturing method.
Key Sectors and Applications
Compression moulding’s ability to produce high-performance, durable components makes it a preferred technique in various industries, especially those that require products to operate in extreme conditions.
- Automotive and Aerospace: Components such as brake pads, friction discs, and other high-stress parts are commonly produced using compression moulding. Thermosetting materials’ strength and heat resistance ensure these components can endure high friction and extreme temperatures without degrading.
- Electrical and Electronics: Compression moulding is widely used to produce insulators, terminal boxes, busbar supports and other electrical components. The process allows for the production of high-quality, heat-resistant parts, which is critical in environments where electrical insulation and fire resistance are vital.
- Marine and Offshore: In environments that demand high resistance to moisture, salt, and pressure, compression moulding is often the go-to process. The marine industry uses this method to manufacture air diffusers and other components that must maintain structural integrity under water pressure and in corrosive conditions.
- Mining and Heavy Industry: Compression moulding is often used to produce parts such as busbar supports and plug insulators used in mining and tunnelling operations. These components must withstand high mechanical loads, short circuits, and exposure to harsh environmental conditions like dust, moisture, and chemicals.
- Hazardous Environments: Compression moulding is critical in producing parts used in hazardous environments, such as micro-switch cases and fuse holders in IECEx or ATEX environments. These environments require materials that can resist both environmental stress and potential explosions, making thermosets an ideal choice.
Conclusion
After over 100 years, compression moulding continues to play a pivotal role in modern manufacturing, particularly for sectors that demand strength, heat resistance, and precision in extreme environments. Its flexibility with thermosetting materials, ability to handle large and complex parts, and cost-effectiveness for small to medium production runs ensure it remains a vital technique.
As industries evolve, understanding the unique benefits of compression moulding will allow manufacturers to make informed decisions, choosing the process that best fits their product and performance needs.
For the British Plastics Federation, it’s crucial to highlight compression moulding’s continued relevance in today’s landscape. Industry leaders must recognise when and where this time-tested technique outshines more modern methods.
Read more from Fairgrieve Compression Moulding here.
Fairgrieve Compression Moulding
0191 415 9292
Website
Email