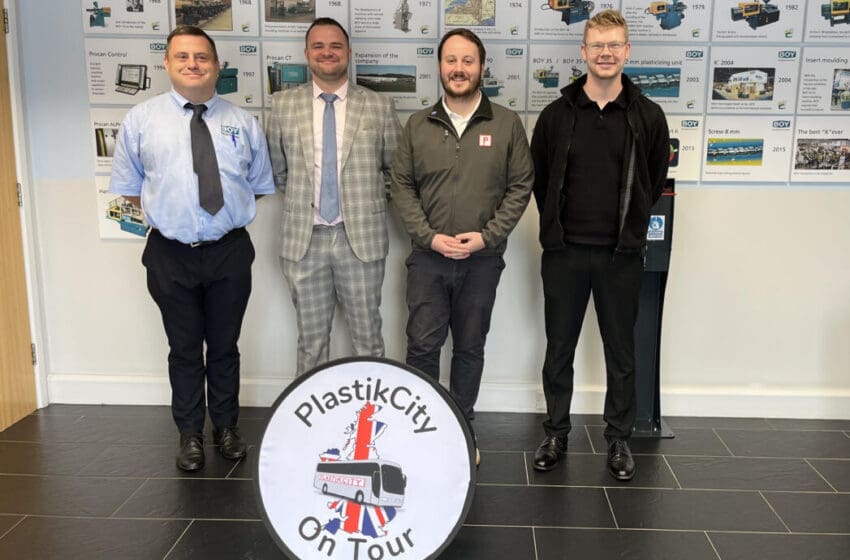
PlastikCity on Tour – BOY Limited
Getting your Trinity Audio player ready...
|
Our next stop was Northamptonshire, where we had the pleasure of visiting BOY Limited, a leading supplier of injection moulding machines. Nestled in Rushden, BOY Ltd has established itself as a pivotal player in the supply of injection moulding machines since Dr. Boy Germany was founded in 1968. BOY’s journey in the UK market began in the early 1970s, and since then, they have become synonymous with quality, efficiency, and innovation in injection moulding technology.
BOY Ltd headquarters in Rushden boasts a state-of-the-art showroom featuring various machines ready for demonstration and sale. This modern facility highlights BOY’s extensive product range and serves as a hub for training and support, as well as tool trials and demonstrations, reflecting BOY Limited’s commitment to customer service and education.
Compact but Mighty
The company’s machinery lineup is renowned for its compact design, energy efficiency, and small carbon footprint. These features are particularly crucial in today’s environmentally conscious market, where reducing energy consumption and emissions is essential. BOY Ltd machines are designed to meet and often exceed these demands, providing customers with solutions that are both sustainable and cost-effective. The company’s uniquely designed servo motor pump drive and cantilevered two-platen locking system are features that enable its extremely compact and space-saving design, marking its product range at the top of the plastics processing industry, particularly in the low to medium clamping force range.
One-Stop-Processing-Shop
Beyond its core injection moulding machines, BOY Ltd can offer an extensive range of ancillary equipment, including dryers, conveyors, server units, chillers, granulators, and material handling systems through its sister company Hi-Class Machinery Ltd. This comprehensive product range reinforces BOY Ltd and HCM Group’s position as a ‘one-stop-shop’ for all its customers’ injection moulding needs.
BOY Ltd is at the forefront of technological advancements with the introduction of Industry 4.0 standard machines. These machines incorporate advanced digital features for improved connectivity and automation, aligning with the latest trends in industrial manufacturing. By integrating such technologies, BOY Ltd ensures that their clients are equipped with the most advanced and efficient tools available enabling greater productivity, data capture and sustainability.
Interview with the BOY Limited Team
Our visit to BOY Limited in Rushden was a valuable opportunity to speak with key team members about the company’s operations, innovations, and future plans. Will Clarke and Matt Matwijczuk from PlastikCity sat down with Liam Price (Service Manager) Michael Wilson (Sales Engineer), and Catherine Baker-Litchfield (Sales & Marketing Administrator) from BOY Ltd to gain insights into what makes BOY a leading name in the injection moulding industry.
Firstly, could you explain the key differences between older machine technology and the modern servo-drive machines you offer?
Liam: Absolutely. For instance, older machines, like those from the 1980s or 1990s, used normally aspirated motors where the oil had to be maintained at 45 degrees for optimal performance. This required significant chilling capacity, essentially heating and cooling of the oil throughout the day, which was quite energy intensive.
Our modern servo-drive machines are different. We only warm the oil to about 25 degrees, just enough to prevent any damage, and the system continuously adjusts itself. This constant recalibration means we no longer need massive chillers, leading to significant energy savings. For example, with our 80-tonne machine, you can reduce electricity consumption by approximately 60% compared to older models.
What is your target market?
Michael: Our target market is quite diverse. We work a lot with the construction, automotive, defence and medical sectors. Recently, the construction sector has been quieter, but automotive and medical have shown some encouraging signs of growth. Research and development applications, along with universities and laboratories, are also significant markets for us. In fact, many universities across the UK and Ireland have our machines in their labs. The small footprint and energy efficiency are perfect for this situation.
Liam: To add to that, other areas are insert moulding and micro moulding, for example. Our machines are suitable for many and diverse applications due to their small footprint and efficiency. They fit perfectly in labs or clean rooms where space is at a premium, and their energy efficiency and ease-of-use is a huge plus for these environments.
How do your machines contribute to reducing the carbon footprint for your customers?
Liam: One of the main ways we help reduce the carbon footprint is through the efficiency of our machines. By not having to heat oil to high temperatures and maintaining it, we significantly cut down on energy use. Additionally, our machines help to prolong the life of the oil used, which means it doesn’t need to be changed as frequently, reducing waste.
For companies aiming for sustainability certifications within the ISO arena, our machines offer a substantial advantage. Essentially, replacing an older machine with one of the new Boy models can instantly reduce the carbon footprint of the products they manufacture, and we’re on hand with aftersales and technical support to enable this transition.
What other products do you provide?
Michael: Besides BOY Injection Moulding Machines, Hi-Class Machinery, BOY’s sister company, offer a comprehensive range of ancillary equipment, including dryers, conveyors, server units, chillers, granulators, and material handling systems. This helps make us a one-stop shop for our customers, providing everything they need to set up or upgrade their moulding operations.
What sets BOY Ltd apart from its competitors?
Liam: Our high level of training and customer service are key factors when deciding on machine supplier. When you buy from BOY, you become part of the “BOY family”. We ensure our customers are well looked after, providing extensive training and support. Our engineers have a broad range of experience and are always ready to assist. Additionally, our machines’ compact size and energy efficiency often surpass those of fully electric machines, making them a very attractive option for many businesses.
What are your plans for the next 12 months?
Michael: We’re planning to expand our product range significantly. While I can’t share specific details just yet, we have some exciting announcements lined up. We are also looking at hosting an open house event to showcase our product range and engage more directly with our customers. Keep an eye out for some exciting announcements in the next few months.
Catherine: We will also be participating in Interplas 2026. We are also considering other events, but nothing has been finalised yet. Exhibitions are a great way for us to connect with potential customers and showcase our latest innovations.
You mentioned Industry 4.0 earlier. How are your machines equipped to meet these new standards?
Liam: Our machines are designed with Industry 4.0 connectivity in mind. This includes advanced features that allow for better integration and automation, helping our customers improve their operational efficiency and data management. These capabilities are increasingly important as industries move towards more automated and connected manufacturing processes and are fully supported by the BOY Ltd machinery range.
Do you have an official company philosophy or mantra?
Catherine: Our slogans are “big name in small machines” and “one-stop ancillary shop.” These reflect our commitment to providing comprehensive, high-quality solutions to our customers and our dedication to being a leading name in the injection moulding industry. Our goal is to ensure that every customer feels supported and valued as part of the BOY family.
Our visit to BOY Limited highlighted not only their technical expertise and innovative approach but also their deep commitment to customer service and sustainability. With plans to expand and introduce new products soon, BOY Ltd continues to be a significant player in the injection moulding sector, with plenty more to come!
Look out for the next edition of ‘PlastikCity on Tour’ to learn more about our excellent UK-based partners.
There are now well over 260 active partners represented on the PlastikCity site, many of which offer highly specialised products or services to our sector.
During our everyday course of business, we’ll be making a point of visiting as many of these partners as we can and using the time to better understand what they offer the market. We’ll then showcase them through this ongoing series of articles.
Maybe you can benefit from their services!
Read more news from BOY Ltd here.
BOY Ltd.
01933 354460
Website
Email