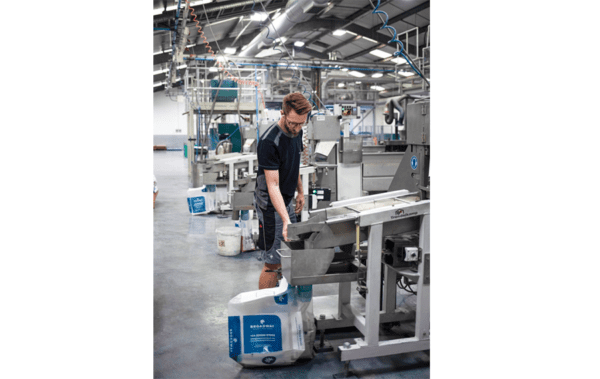
Broadway’s MasterFoam – One Additive with Many Benefits
Broadway’s blowing agent masterbatch was extensively trialled throughout 2023. The material – developed by Broadway’s in-house technical team, is now being marketed as MasterFoam. Moulders using the additive have achieved notable reductions in polymer usage, cycle times, costs, and the light-weighting of their components.
How Does it Work?
Broadway’s MasterFoam is a chemical foaming agent (also known as a blowing agent). MasterFoam instigates a reaction, creating a foaming effect while the material is liquefied during moulding. The foam expands as the thermoplastic cools in the mould. This process offsets the tendency for the moulded part to shrink whilst cooling, thus reducing sink marks. As the material hardens, a fine, regular foam structure forms within it, reducing its density. This means less polymer is needed to fill the mould cavity. Therefore, less material is required to complete the production run, reducing material costs by almost 10% in many instances. As a result, the moulded component is lighter, which, of course, offers obvious advantages in many different applications.
MasterFoam is an endothermic blowing agent. Endothermic blowing agents absorb energy during the reaction process, so the reaction is easy to control. They typically only release carbon dioxide and water upon decomposition. Broadway states this is much safer than widely available exothermic blowing agents.
The viscosity of the MasterFoam melt is lower than that of polymer on its own. This is due to bubbles beginning to form in the melt, allowing for deformation. This lower viscosity results in a smoother, quicker injection stage. Shot speed is increased as the polymer must be ‘short shot’ into the mould (i.e. less polymer added) to allow a uniform expansion of the foam in the mould. Cooling times are typically reduced, contributing to reduced cycle time, energy demand and costs.
In extrusion moulding trials, the use of Broadway’s extrusion grade additive (MasterFoam-Ex) doubled the running speed of a customer’s extrusion. This effectively doubled the capacity of their operation without any capital investment in upgraded infrastructure. The reduced component weight was also highly beneficial for their application. Broadway suggests that the potential for this customer is huge.
Another advantage is that the open-cell structure offers improved acoustic and thermal insulation properties. This would be particularly beneficial in applications such as window frame profiles. Components used in construction are increasingly scrutinised for thermal efficiency.
What are the benefits?
MasterFoam offers many benefits. The application, polymer type and moulding conditions will determine which are achievable and to what extent in each moulding.
Following successful trials, an industry partner’s projected figures suggest they could save 105 tonnes of polymer over five years in just two small packaging components moulded for a leading multinational consumer goods company. They state this would result in a saving of £110,000 on material costs alone. For packaging components subject to the UK Plastic Packaging Tax (the rate of which is due to rise again in April), MasterFoam offers a further cost-benefit due to the reduced volumes of polymer processed.
Summary of MasterFoam benefits:
- Reduction in weight of the moulded component
- Reduction in material usage
- Reduction in costs, without any tooling changes
- Reduced cycle times
- Reduced energy demand
- Reduced carbon footprint of the component
- Increased shot/running speed
- Increase in productivity (up to 100%)
- Prevention of sink marks in the moulded component
- Improved strength-to-weight ratio of the component
- Improved thermal efficiency of the component
- Improved acoustic insulation of the component
Trial Results
Over the past year, Broadway conducted a series of trials with different moulders. These covered various end applications in injection moulding trials using MasterFoam and MasterFoam – Ex. See the table below showing a summary of results from some of the trials carried out in 2023
Trial Date | February 2023 | August 2023 | October 2023 | November 2023 | November 2023 |
End Component | Overcap for detergent bottle |
Faceted jar outer | Thick-walled jar lid, used in cosmetics |
Plastic pallet | 20M decking board, for use on superyachts |
Moulding Process | Injection | Injection | Injection | Injection | Extrusion |
Additive | MasterFoam | MasterFoam | MasterFoam | MasterFoam | MasterFoam–Ex |
Polymer | PPHO | PPHO | PPHO | Recycled PPHO | Flexible PVC |
Addition Rate | 0.5% | 1% | 0.5 – 1% | 0.5 – 1% | 1% |
Weight Change | 7.6g > 7.0g | 39.9kg > 36.3kg | 16.6g > 15.0g | 14.5kg > 13.4kg | 6.4kg > 3.2kg |
Weight Saving | 7.9% (0.60g) | 8.9% (3.54kg) | 10.0% (1.64g) | 6.6% (1.09kg) | 50% (3.20kg) |
Time reduction | Reduced cycle time by 6% (From 16.6s to 15.6s) |
Reduced cycle time by 6.4% (From 15.7s to 14.7s) |
Reduced cycle time by 9.4% (From 6s to 5s) |
Reduced cycle time by 9.9% (From 116.7s to 105.15s) |
Doubled running speed! |
Notes | Passed QC check and no detrimental effect when colour masterbatch was added (a gold pearl). | No negative effect observed during QC or when colour was introduced. | No negative effects on dimensional properties were observed during QC checks. | An additional 27 pallets could be manufactured during each 8 hour shift. Improved productivity will increase revenue. |
This trial utilised our extrusion grade blowing agent. The potential benefits for this customer are huge – reducing costs and doubling their production capacity. |
As you can see from the table of results, Broadway’s blowing agents have proven to offer a multitude of benefits in both injection and extrusion moulding processes at low addition rates. Supplied in masterbatch form, the cost of the additive is less than the value of the polymer saving it provides, so it has a real commercial appeal. The more a customer uses, the more they’ll save! And this is before any additional savings in energy, production efficiency, transportation and tax are considered.
Why Use Broadway’s Blowing Agents?
Broadway’s injection-grade chemical foaming agent – MasterFoam, is not an imported or traded masterbatch. It was developed in-house by Broadway’s technical team. It’s a made-to-order material manufactured in the UK, offering fast turnarounds and security of supply. In 2023, MasterFoam produced the best results in independent trials against a number of competitor blowing agents. Broadway has vast experience in manufacturing colour and additive masterbatches and compounds. Their 90,000 ft2 facility in Suffolk also provides their technical and sales support.
Broadway recommends running a material trial to see the benefits for yourself. They’re currently offering free samples for line trials and they’ll even provide expert technical support to help you achieve the optimum results.
To learn more or to request a free trial of Broadway’s MasterFoam, please get in touch using their website, email or call.
Dr Stephen Rayner, Technical Manager at Broadway, said:
“Broadway’s MasterFoam allows our customers to achieve ‘more for less.’ This product saves weight significantly in the final moulded component, meaning less polymer is required. We’ve been delighted with the results we’ve seen from customer trials over the past year.”
“We’re continuing our sustained effort to expand our product portfolio with new offerings which support customers in achieving their commercial and sustainability goals.”
Read more news from Broadway here.
Broadway
+44(0)1986 875 100
Website
Email