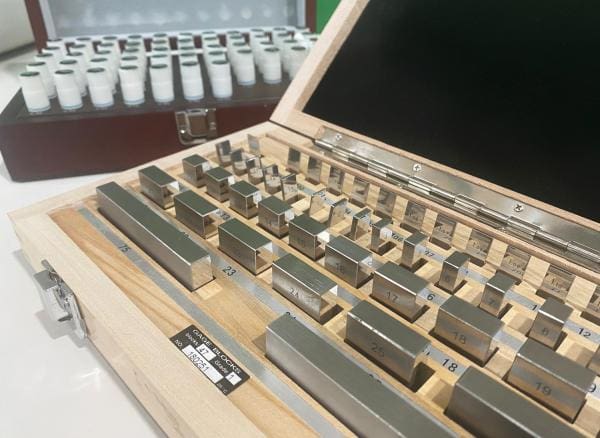
Quality & Validation on 3D Printing | 3DPRINTUK
As additive manufacturing (AM) / 3D printing gains more and more traction as a production technology, scrutiny of the end products produced by the process becomes more and more intense.
When the 3D printing process is used to make prototypes, small deviations from the original design intent are not ideal, but at the same time, are not disproportionately important. However, when the parts produced need to perform an end-use function, occasionally in mission-critical applications, verifiable conformance with design intent is vital, as is the maintenance of an accredited quality system to ensure minimum levels of performance and repeatability.
In this article, we get a behind-the-scenes perspective on quality and validation from Alessandro Catania, Quality and Compliance Manager at 3DPRINTUK. Catania responds to various questions and reveals the importance of expert engagement with a 3D printing expert early in the design process to ensure optimal outcomes.
3DPRINTUK specialises in low-volume production using state-of-the-art powder bed fusion (PBF) 3D printing systems with polymer materials.
Q. We understand that 3DPRINTUK is working towards ISO 9001 accreditation. Can you outline the process you are going through?
AC. For years we have been building an incredibly in-depth order management system that tracks all aspects of a customer’s order progress. Since the beginning of the year, we have slowly but confidently built a Quality Management System (QMS) fit for ISO 9001:2015 accreditation on top of the existing system. We have just recently passed the Stage 1 audit with flying colours. Neither non-conformance nor observations were raised during the audit, which means that full accreditation is almost certain before the end of the year.
Q. What are the main takeaways for a customer when you get ISO accreditation?
AC. For our smaller clients (generally hobbyists) who may or may not understand what ISO 9001 entails, the main takeaway is that they can have more confidence in our services, knowing that their parts are being printed to the highest quality standards. For the larger OEMs in our customer base (especially those who already have the standard), gaining ISO 9001 is a further assurance that their supplier has all the right quality assurance checks in place to deliver the right parts on time every time.
Q. How easy is it to spot potential quality issues with such a high number of printers?
AC. We feel that the depth of our in-house QMS is unrivalled in the industry. The in-depth non-conformance side can monitor stats generated from failed parts and identify trends in said non-conformances at lightning speed. This allows us to evaluate, identify and eliminate any machine issues much faster than we used to, massively reducing the impact of any potential manufacturing problems from almost any machine.
Q. When looking at customer builds, what are the main quality concerns you are looking for and do they vary from process to process?
AC. Surface finish, strength and dimensional accuracy are the three main factors determining a conforming part for us. The parts we print are all visually inspected after the build, after each post-processing stage, and again one last time before shipment. We print between 80,000 and 90,000 parts every month, so we know that sometimes a small blemish can be missed, which is why components are checked so many times. Each build also features a printed quality control sample that is measured to give us assurance on the general dimensional accuracy of the parts. If any of the dimensions of the sample are outside specific tolerances, then we measure all the parts in the build before shipment.
Q. What sort of tolerances can be attained, and how far do these tolerances need to slip before a part is rejected?
AC. We guarantee a maximum tolerance of ±0.3 mm up to 100 mm, and 0.3 mm for anything more significant. Most of the parts we print are well within ± 0.15 mm. We also have a minimum guaranteed thickness of 1 mm for any printed part, which increases to 2 mm if there are any post-processing requirements.
Q. What sort of yield does 3DPUK attain on the different processes?
AC. We monitor our yield by tracking the Right First Time KPI. MJF is our most reliable technology, with a RFT score in the high 90s. SLS is a slightly more temperamental process but not far off from MJF. We constantly monitor part failure data, and we have noticed that a major contributing factor to part failure is a lack of DfAM knowledge. We often receive designs that aren’t quite suitable for our processes, and this results in part failures, and the rebuilds ultimately affect our RFT score. Lack of DfAM knowledge is, unfortunately, a common issue in our industry. Still, we are confident that our yield would be significantly higher by raising awareness of a few DfAM principles. We have already started by publishing a short 3-part DfAM guide on our blog; however with the upcoming website update, we aim to share more helpful information and design guides with our customers.
Q. When it comes to Design for Additive Manufacture (DfAM), what are the main issues?
AC. DfAM requires a different approach compared to traditional manufacturing and assembly design (DfM&A). The latter focuses on designing products so that manufacturing and assembly costs and difficulties are reduced. At the same time, DfAM aims to capitalise upon the unique capabilities of AM to design and optimise a product or component, thereby promoting innovation. The key here is the utilisation of the characteristics of AM to improve product functionality according to the capability of the AM process. This typically indicates that designers can tailor their designs to utilise the advantages of AM for complex geometries and light-weighting opportunities whilst considering the AM process limitations to ensure the manufacturability of the product. New flexibilities in design are a key benefit of 3D printing. However, it is not without its restraints, which is why specific DfAM skills are essential to successful adoption. As with any manufacturing process, there are good designs, and there are bad designs, and understanding this is essential for successful outcomes. For many design engineers and manufacturers, however, this is a leap into the unknown and can be a barrier to adoption.
Q. Is it fair to say that quality issues are one of the most fundamental brakes on using 3D printing as a production technology?
AC. I guess so. To produce high-quality, 3D printed parts, several challenges need to be mitigated. The quality of powder used can be a big determining factor when it comes to outcomes, so we need to monitor for contamination and moisture content etc… and how the material is transported, stored and handled. Also, we need to monitor process control from engineering into production and beyond post-processing. So much in this chain can affect the quality of outcomes, from internal machine issues such as laser path and intensity to the design of support structures. These issues can be difficult to address and standardise build-to-build without good quality control and quality assurance methods. You can end up with an inefficient, potentially expensive, and time-consuming trial and error approach that ultimately ends up countering the key benefits of 3D printing, namely the timely, cost-effective production of small batch geometrically complex parts and components.
Q. And there is always the human factor to add to the mix?
AC. For sure. Humans introduce mistakes, and the human influence in the 3D printing process chain is disproportionately high initially in design, setting process parameters, then manual checks during printing, inspection before post-processing, and of course, during post-processing. Manual involvement in assessing quality indicators can impede the quality and repeatability of outcomes.
Q. And the answer?
AC. To clear the path to the easy adoption of 3D printing for industrial production, it must be acknowledged that these issues, first and foremost, really do have to be addressed. Quality management in 3D printing needs to be discussed with an end-to-end approach, first looking at material, then DfAM, build parameters and build, and then post-processing. How rigorous this approach is, is driven to a large extent by the specific applications and the required level of precision and accuracy. The focus is quality assurance in design and build instead of just focusing on the quality of the part produced, as would be the case in traditional manufacturing processes.
It’s not simple, and it is a reason that so many companies lean on subcontracting 3D printing specialists such as 3DPRINTUK, as we live and breathe these technologies and obsess about quality, reducing the headaches for our customers. 3D printing is already becoming an important technology that is disruptive across numerous industrial sectors. I hope I have shown how a fundamental end-to-end focus on quality assurance is key to increasing its level of adoption.
Read more from 3DPRINTUK here.
3DPRINTUK
+44 (0) 208 692 5208
Website
Email