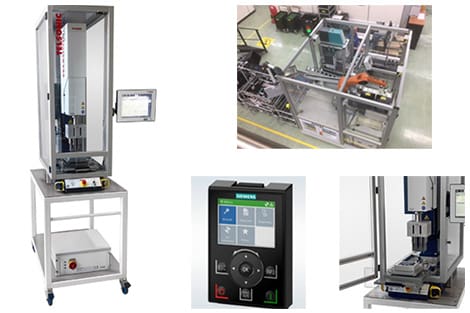
Siemens Boosts Inverter Panel Production with Telsonic Ultrasonic Technology
Siemens recently turned to Telsonic UK for its latest ultrasonic welding solution to support a new Total Productive Maintenance (TPM) programme and production line upgrades aimed at increasing production capacity.
As an existing user of Telsonic’s ultrasonic welding technology, Siemens Congleton has long benefitted from the process to manufacture its intelligent variable speed drive controller products.
At the stage in production where the welding must take place, the Siemens operator panel comprises three main components: polycarbonate front and rear housings and a PCB. The assembly and subsequent welding of the rear housing to the front housing encapsulates and secures the PCB within the assembly. Using ultrasonic welding as the joining method means it is essential that the energy is directed into the joint and not allowed to dissipate into the surrounding features, which secure the PCB within the assembly.

The original and highly successful Telsonic USP3000P welder was integrated as part of a robotic manufacturing cell that moves the product between a programming station, welding station, quality check and packaging station.
The latest generation USP3000E welder, which now replaces the original unit within this cell, is based around a 20kHz, 3.6kW ultrasonic welding system, complete with electronic proportional pneumatic control and a linear encoder, a configuration which allows the weld collapse height to be measured and controlled precisely. This guarantees that no excess energy is transmitted to other areas of the casing or the PCB beyond the full collapse of the energy director weld feature moulded into the parts. New features of the USP3000E product include Telsonic’s new Telsoflex touchscreen interface control system offering ease of use, intuitive setting and results display, plus the latest MAG generator technology and advanced data streaming output.
cell used to produce the IOP/BOP controller range
Siemens has also invested in a second USP3000E system, configured as a turnkey manual welder, to provide the additional capacity needed to meet expected volume increases for the Siemens IOP/BOP controller range. This system will also serve as a backup for this important production line.
Both welders have interchangeable tooling and are identical with part presence sensing incorporated within the fixtures, which are mounted on sliding table assemblies for either robot or manual loading.
Each part fixture incorporates features to facilitate robot end of arm gripper access and has simple replaceable inserts to protect the highly finished surfaces of the IOP/BOP range. Each welder is programmed with weld quality limits and they are interfaced using OPC/UA to Siemens data collection and product barcode with weld data for every product stored to allow full traceability and quality control.
The reason for Telsonic‘s continued supply success with Siemens Congleton has been the performance of the original USP3000 series welding system over a period of 12 years combined with the service from Telsonic UK to support exacting products and process control standards. Confidence in the use of ultrasonic welding technology by Siemens Congleton has increased significantly during this time with its resultant benefits of speed, cleanliness and consistency.
Telsonic UK offers a comprehensive range of ultrasonic modules and systems for various plastic welding, cutting, sealing, cut’n’seal, food cutting, metal welding, packaging, sieving, and cleaning applications within a wide range of industries. Visit www.telsonic.com to find out more or get in touch with the team using the below contact details.
Telsonic Ultrasonics
+44 (0)1202 697340
Website
Email