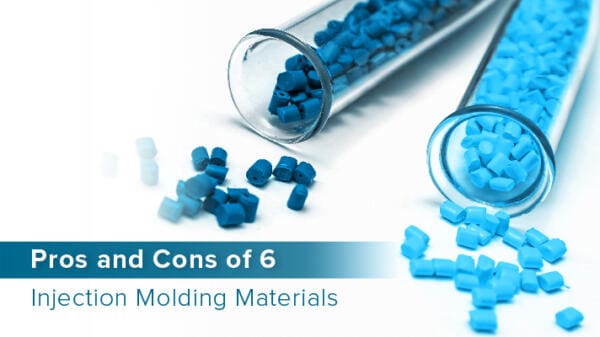
Pros & Cons of Six Injection Moulding Materials
In this blog, RJG Technologies examines the pros and cons of six common injection moulding materials, including Polypropylene, Polycarbonate, Polylactic Acid, Acrylonitrile Butadiene Styrene, Polyethylene and finally, Polyamide.
One of the first decisions that needs to be made when designing a new injection moulded part is which material to use. The material (and additives) you choose has a huge impact on how the plastic will flow through the mould, what the process will be, and the look and feel of the final product. Here are some pros and cons of six well-known injection moulding materials.
1. Polypropylene (PP)
Polypropylene is one of the most popular materials for injection moulding because of its mouldability. It is versatile, offers a wide array of uses, and has various unique properties that make it an attractive option. Even though PP has a semi-crystalline nature, it has a low melt viscosity, which allows it to flow extremely well. That means you can fill the mould much more quickly, cutting down production time for each shot.
PP is also a relatively inexpensive material, making it cost-effective. It is very resistant to moisture, has good chemical resistance, good impact strength, and is a good electrical insulator.
There are a few shortcomings, however. It has a high thermal expansion coefficient, which means it is limited in high-temperature applications. It is susceptible to ultraviolet degradation and has poor resistance to chlorinated solvents, is difficult to paint due to poor bonding capabilities, is highly flammable, and is susceptible to oxidation.
2. Polycarbonate (PC)
Polycarbonate is one of the strongest, most durable materials, making it ideal for face shields, visors, or safety glasses. It is a naturally transparent amorphous thermoplastic, which means it remains transparent even if colour is added, similar to glass. PC has great heat resistance properties and can be combined with flame retardant materials without material degradation.
PC also has high thermoplasticity, which means you’re able to melt, cool, and reheat it without material degradation. This allows it to be injection moulded easily and, later, recycled. It is a pretty pliant material, so you can form it at room temperature without it cracking or breaking. The amorphous properties mean they gradually soften instead of quickly transitioning from a solid to a liquid.
There are a few areas where PC falls short. It is more susceptible to scratching, even though it is a highly durable substance. That’s why it is encouraged to apply some kind of scratch-resistant layer in order to protect it on clear substances, like shields or glasses. PC is considered toxic when it comes in contact with food due to its release of BPA during degradation. There are many options today that are BPA-free, however, for use in food and water applications.
3. Polylactic Acid (PLA)
Polylactic acid is a bio-degradable plastic manufactured out of plant-based materials, like corn starch or sugar cane. That’s why it is known as “the green plastic” or “bioplastic.” If you add in a filament recycler, you’re about as green as you can get. PLA is mostly used for food packaging, bottles, film, and medical supplies.
PLA is biodegradable and has characteristics similar to PP and polyethylene (PE) and is a bit more brittle than acrylonitrile butadiene styrene (ABS). It constricts under heat, which makes it highly suitable for applications such as shrink wrap. PLA melts very easily, making cycle times shorter. It is not toxic and safe for food handling and medical implants.
Due to its low glass transition temperature, PLA is unable to contain hot liquids or other high heat applications, even a hot car in the summer. PLA is also slightly more costly than other options and can be more difficult to colour.
4. Acrylonitrile Butadiene Styrene (ABS)
Acrylonitrile butadiene styrene is an extremely popular middle-of-the-road injection moulding material due to its balanced combination of mechanical toughness, wide temperature range, good dimensional stability, chemical resistance, electrical insulating properties and ease of fabrication.
ABS is available in a wide range of grades and textures, including high-impact, heat resistant, fire-retardant, and high gloss. It is a tough, rigid material and metal coatings easily adhere to it. Plus, it looks great and can be very easily processed—it flows well and easily releases from the mould.
There are some downsides to ABS, though. It has poor solvent resistance and poor weatherability, but there is a UV additive that can improve that problem. ABS is also a poor electrical insulator and melts very easily (even when you don’t want it to).
5. Polyethylene (PE)
Polyethylene injection moulding material is the most popular and commonly used plastic in the world, used in shopping bags, toys, garbage cans, and shampoo bottles. It is a lightweight thermoplastic material that has high chemical resistance, elasticity, and electrical insulating properties. PE has low hardness, so it is very ductile and has good impact strength, meaning it will stretch rather than break.
PE is water-resistant and durable with high weatherability. Depending on the material’s thickness, it can be transparent to opaque, making it suitable for packaging applications. It can be easily recycled into other products, which is more cost-effective than using new plastic.
The downside to PE is that it is not environmentally friendly. It takes a long time to break down, which means it could be in landfills for decades. It can also be toxic if it is incinerated, which is another means of disposing of plastic waste. PE is extracted from petroleum, or natural gas, which is a limited resource. The production of PE releases high greenhouse gas emissions of carbon dioxide, contributing to global warming and climate change. Sorting through the various types of PE to recycle it is complex and expensive.
6. Polyamide (PA)
Polyamide, also known as nylon, is a semi-crystalline polymer with a good range of properties. It is tough and has a high melting temperature, good wear, and chemical resistance, so it is a good option for strong mechanical parts, such as bushings, gears, and bearings.
PA has a high-temperature endurance for a short period of time. It is tough enough to withstand repeated impact. Its tensile strength is more than twice as high as ABS and is higher than that of metal, and its compressive strength is comparable to metal. It has a high resistance to abrasion and wear. When used as a movable mechanical part, PA is self-lubricating with low noise, and its smooth surface leads to very little friction. PA is also non-toxic, odourless, self-extinguishing, inert to biological erosion, antibacterial, anti-mildew, and has great weatherability.
The cons to PA are that it absorbs moisture, which can affect the electrical and mechanical properties, especially in thin-wall applications. This requires strict requirements for injection moulding due to the need to ensure no moisture enters the part and the difficulty in controlling dimensional stability due to thermal expansion. Uneven wall thickness will cause distortion and deformation. It also requires UV stability due to its poor resistance to light, turning brown and then cracking when exposed. PA can also be attacked by strong acids or bases, causing material degradation and making it unable to be used as an acid-resistant material.
Summary
There is no perfect polymer. The key is determining which qualities are most important to you and which qualities you absolutely do not want.
If you would like assistance choosing the right resin for your application, get in touch with RJG Technologies using the contact information below.
RJG Technologies
+44 (0)1733 232211
Website
Email