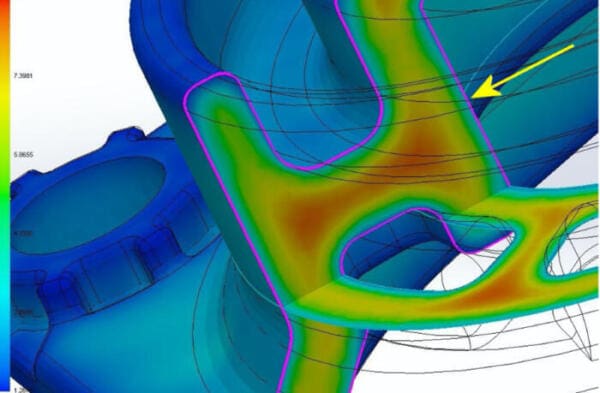
How to Gain Major Advantages for your Plastic Parts
In this blog from the ENL Group, you’ll learn the tips and tricks that will help you gain advantages when it comes to specifying polymer for your parts, and how to avoid costly mistakes.
Engage your supplier as early as possible and establish a partnership
Concept or quotation stage is definitely not too early. This is where you should engage with a partner and not just a supplier. By doing this you will gain many advantages including: making the most of your partner’s experience and expertise; ensuring a smooth transition from design into production; accessing their supply chain and logistic sources; they can gain more in-depth expertise and advice; harnessing the potential to save time and cost as design advise will be available; defining the feasibility of the material by using simulating software; defining the tool requirements early; specifying and selecting the right polymer and beating your competitor to market.
Consider where the part will be used and what conditions it will be exposed to
There are certain polymers required for specific applications, so understanding what it will be used for, what conditions it will be exposed to and what temperature range, is extremely important to understand at the start of the process, in order to specify the right polymer. This opens up new areas for consideration such as flammability, as well as specific industry standards for polymers, as some companies will only accept polymer made parts from a list of pre-approved and accredited polymers.
Is the part driven by cost or product performance?
Knowing the answer to this question will help determine the range and types of polymer that can be considered for your project. Other factors that will influence the decision-making and feasibility of polymer selection include requirements around minimum order quantities, colour and lead times. It definitely pays to understand challenges at the start of a project, rather than facing – often costly – challenges later down the line.
Work with a supplier who can assess the feasibility of your part
When the moulding accuracy for your part is critical, when tolerances are tight, and there is no margin for change, you need to work with a moulding supplier who has design capabilities. They use high-tech specialist software that will render a part and explore, in further detail, the intricacies of a material, and will predict shrinkage, warpage, material flow and other material/part specifics. The software enables a supplier to quantify such issues and implement the necessary changes – either to tooling or material – before the part goes to production. This saves significant time and costs.
Learn the different types of thermoplastics
If you’re trying to choose a grade, referring to a simple chart that highlights the different grades of thermoplastics. The IAPD thermoplastics rectangle is a good tool to refer to, which splits the two types of thermoplastics – amorphous and semi-crystalline – into the different categories.
You can download the guide here.
Ensure you’re partnered with a credible supplier
If you have a good moulding supplier, they will have access to a strong supply chain, giving you access to a wide range of high quality, specialist polymers as well as a wide range to fit different pricing requirements.
Could your metal part be plastic instead?
A great example comes from within ENL Group working with a large aerospace customer on a metal replacement programme. This programme so far has saved over 70% on weight, which directly led to fuel savings and carbon emission reductions. Material cost saving against titanium has been over 60%, and further savings were made against the percentage of waste that was incurred on the original machining process, with an optimised polymer design that utilises minimum material. Manufacture time was reduced from 30 minutes down to one minute. In some cases, the labour cost was able to be reduced as the parts manufactured were moved away from being bespoke, ‘one-off’ parts to being repeatedly batched.
With repeatability assured, part measurement was also reduced. One part per batch is now measured, as opposed to each machine part. We are using a statistically controlled process to ensure repeatability. Parts are continually formed in the same approved mould without the reliance on cutters or moulding and without the need for manual input. Finally, there is no need for painting and finishing, as there is with metal and aluminium (to prevent corrosion) as plastic parts are inert.
Consider a hybrid solution
Metal parts can be over-moulded with plastic, to produce a cheaper, lighter and more repeatable components. You can insert areas for high wear, accuracy, bearing joints, threaded inserts (there’s often a need for threads to be within plastic moulding). This is something that can be taken advantage of – it’s more cost-effective and stronger than a separate secondary operation, and it’s cheaper for tooling than an expensive action-driven tooling solution. Copper over-moulding is another example, big in the automotive sector, something the ENL plant in Slovakia does a lot of. Finally, don’t discount plastic over plastic either – all of these are possible and will usually save a company time and cost.
There are specialist grades for metal replacement. Our partner, Hardie Polymers, has a guide to their polymer range, which can be downloaded here.
Some of the grades include special weight-saving polymers (that can save up to 20% weights), high-gloss finishes (to replace paint finishing), scratch-resistant polymers and grades with renewable and natural fibres.
Recycled plastics can be high in quality and low in cost
Not every industry or application allows for recycled plastic, but if it does, then this isn’t something you should shy away from. There is plenty of very good, high quality, recycled polymer that is used by some of the major car brands in automotive today. Not only are these materials delivering on performance, but they are also saving customers up to 20% in costs.
For more information about ENL Group, or if you’d like to discuss your requirements, please get in touch.
ENL Group
01275855207
Website
Email