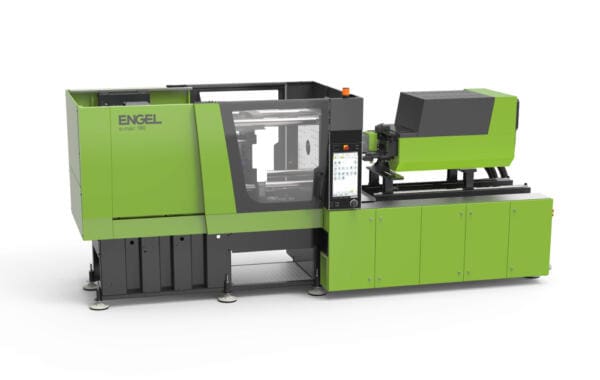
ENGEL e-mac: Compact, Flexible and Cost-Effective
In October 2020, ENGEL is presenting the next generation of its all-electric e-mac injection moulding machine series in a challenging application for the manufacture of pipette tips. Offering maximum flexibility for individual customer requirements, the e-mac is now even more compact.
The quality of pipette tips largely depends on the precision of the injection process. At the same time, the long cores in the mould require precise movements of the mould mounting platens during opening and closing. All-electric injection moulding machines are, therefore, the preferred solution in this application segment, where cost-effectiveness is a decisive factor in choosing a machine.
In the form of the e-mac, ENGEL has an all-electric injection moulding machine in its portfolio that combines high output and energy efficiency with extremely compact machine design, ensuring the lowest possible unit costs even in a clean-room environment. ENGEL has now reduced the footprint of the e-mac machines even further. Thanks to an optimised toggle lever geometry, the e-mac 265/180 presented for market launch is 450 mm shorter than the previous 180-ton version, without reducing the opening stroke. Among the all-electric machines on the market, the e-mac machines of the new generation are the most compact worldwide in their respective performance segment across the entire series.
All movements of the ENGEL e-mac – including the nozzle movement and ejection – are performed by servo-electric drives. This means that the machine achieves very high overall efficiency. If required, a servo-hydraulic unit can be integrated into the machine frame without requiring additional space.
The ENGEL e-mac injection unit was developed from scratch with a focus on even better dynamics. It is available in three performance classes. As a result, the machine can be precisely adapted to requirements in order to achieve the highest overall efficiency for the widest variety of applications.
Fully automated on the smallest footprint
The e-mac 180 is demonstrating the performance of the next generation machine with the production of pipette tips made of polypropylene in a 64-cavity precision mould by Tanner (Feuerthalen, Switzerland). The cycle time is six seconds, which is exactly the range in which the e-mac machines fully play to their strengths. For precision applications with cycle times of more than four seconds, the e-mac is often the most economical solution in the field of all-electric injection moulding machines. Apart from medical technology, the machine is deployed in the fields of packaging, teletronics and technical moulding.
The automation makes an additional contribution to the very small footprint of the production cell on show. An ENGEL viper 20 linear robot removes the 64 pipette tips from the mould and transfers them to the integrated compact cell for cavity-sorted depositing. ENGEL’s new automation cell can be custom designed. It houses all automation components and downstream process units, such as quality control, a tray server or box changer, and is significantly narrower than conventional safety guarding. Its standardised build-up allows for speedy mould set-up of the production unit in case of a product change.
Smart assistance boosts process consistency
On customer request, ENGEL supplies production cells that are precisely tailored to the application and include solutions for digitalisation and networking in addition to the injection moulding machine and automation. For the production of pipette tips, the production cell is equipped with the iQ weight control and iQ flow control smart assistance systems.
While iQ weight control readjusts the melt volume for each individual shot, ensuring consistently high quality of the injection moulded products, iQ flow control automatically adjusts temperature differences in the cooling water manifold circuit. To do this, the software uses the measured values determined by the e-flomo temperature control water manifold system. This results in constant temperature control conditions and significantly improved energy efficiency, as the speed of the pumps in the ENGEL e-temp temperature control devices is also automatically managed to reflect requirements.
ENGEL
+44 (0) 1926 335000
Website
Email