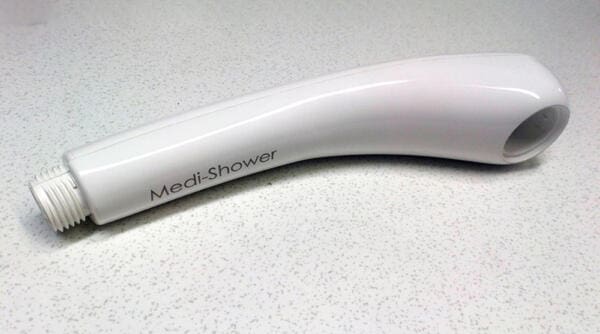
Telsonic Shower Whale Pumps With Weld Success
When Whale Pumps, a Northern Irish manufacturer of pump products and heating systems, developed a new specialist shower system for the medical market, they turned to Telsonic‘s ultrasonic welding technology for the required critical joining operations.
Whale Pumps manufactures and supplies a wide range of freshwater, bilge, and waste pump products and heating systems for the marine, caravan, motorhome, healthcare, and industrial sectors. An important area for growth for this Northern Ireland based business is the expansion of their technical services offering – which includes injection moulding, design, and manufacturing expertise. This has been possible with their help in developing an innovative new product within the medical market, in the form of a specialist Medi-shower system for use in hospitals and patient care environments. This patented anti-microbial showering solution enables institutions to reduce the risk of water-borne infection and offers a standard showering option for all healthcare organisations.
As part of the manufacturing process, a series of weld operations are required to assemble and join the individual showerhead moulded components. The quality and aesthetics required on this product were key criteria in Whale selecting Telsonic’s ultrasonic welding technology for the application.
This innovative product comprises a three-part ABS moulded handheld showerhead assembly, with bayonet located interchangeable nozzle cartridges. The first weld to be performed in the assembly sequence seals the inner water feed tube, which runs from the threaded shower hose connection point to the shower nozzle chamber on the outer half of the head. This is followed by a second weld that secures the inner cover moulding, completing the full showerhead assembly process. The weld joints for all parts feature a tongue and groove section combined with an energy director preparation incorporated in each of the three mouldings, as recommended & designed by Telsonic UK.
The ultrasonic welding solution supplied by Telsonic UK, which is now in full production, comprises a machine and a suite of two toolsets for the three part ABS Medishower spray head. The ultrasonic welding process was determined as the most suitable following a DFMEA appraisal. The short process welding time, plus the ability to both join and achieve a robust hermetic seal, with high process repeatability using moulded weld features alone and eliminating the need for adhesives or mechanical seals, clearly identified ultrasonics as the process of choice.
The configuration of the production system included a Telsonic USP3000 – 20kHz 2kW ultrasonic press complete with two sets of CAD machined hard anodised slotted aluminium block sonotrodes and CAD machined anodised tooling nests set onto precision levelling plates. Subsequently, a second USP3000 press – 20kHz 3kW system has been purchased.
The challenge in this application is to complete the welded assembly with no gaps or flash on the exterior outer joint line, without marking the highly polished outer shell halves to provide a superior aesthetic finish. In addition, the welded joints need to achieve a hermetic seal, especially between the feed tube and outer half of the moulding, which are pressure tested. The inner tube component and outer shell half also each incorporate half of the shower hose thread section, making it important for the joint design to accurately align the thread form and weld without producing flash.
To achieve this weld cycle, Telsonic devised a time-based weld, split into three-step pressure profiled stages, with concurrent amplitude profiling. This was achieved using the USP3000 proportional pneumatic valve control together with the machines digital generator system to control the melt, with a progressive and optimised energy draw.
Telsonic UK was selected for this application based upon the company’s reputation for delivering robust and reliable ultrasonic welding solutions, combined with their pro-active input at the design stage and experience with similar high quality and demanding applications.
Telsonic UK offers a comprehensive range of ultrasonic modules and systems for a variety of food cutting, plastic welding, cutting, sealing, cut’n’seal, metal welding, packaging, sieving, and cleaning applications within a wide range of industries.
Telsonic Ultrasonics
+44 (0)1202 697340
Website
Email