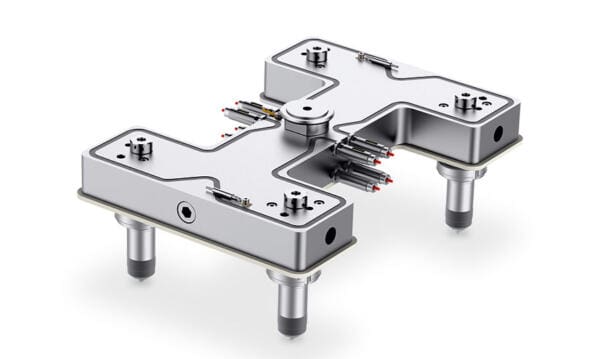
Higher Quality Thanks to Gentle Flow – Intelligent Manifold Technology from GÜNTHER
GÜNTHER, a leader in the field of hot runner technology, will present the optimal design of its manifold technology at the K Show 2019 in Düsseldorf.
GÜNTHER presents its manifold technology at the K in Düsseldorf
High product quality and a safe injection process with the shortest possible cycle time are what every plastics processor strives for. The key to this lies in the tools. This requires a combined effort from manufacturers of system components, such as hot runner systems, as well as mould makers themselves. Intelligent manifold technology offers an advantage.
GÜNTHER, known as a technology leader in the field of hot runner technology, will highlight the optimal design of its manifold technology both in regards to its rheological and thermal properties at the world’s largest plastics trade fair, the K-show 2019 in Düsseldorf.
Melt flow with no edges or corners
Ensuring consistent component quality while taking economic aspects into account is not always easy. Short cycle times and thus rapid solidification of the melt are strived for, while all cavities in the mould must be evenly filled to meet a broad spectrum of quality requirements. Here, the manifold system plays a crucial role, ensuring that the moulding material flows with as close to the same pressure and the same melt state as possible into each of the individual mould cavities. Imbalances often arise due to uneven melt flow behaviour. This can be caused by differences in pressure, temperature and melt viscosity. The viscosity of plastics is influenced by the shear rate and the temperature. As the shear rate or temperature increases, viscosity decreases. However, intelligent manifold technology, the deflector and the contour plug can influence filling processes and ensure more uniform flow behaviour. For this, hot runner system knowledge is essential, of which the manifold is an important component.
Specialists from GÜNTHER address customer needs on an individual basis and design the manifold according to the flow requirements of the respective plastic types. GÜNTHER also offers a large number of standard manifolds, such as straight manifolds, H and T manifolds as well as cross and star manifolds in its portfolio, which can also be individually adapted to customer requirements based on semi-finished products prepared in a modular system.
Individual standard solution for high product quality
To obtain high-quality products at the end of an injection moulding process, technical expertise in tooling and mould making as well as for the respective requirements of the production processes is required. GÜNTHER is versed in the requirements of a wide variety of industries and is constantly working to advance high-quality, precise and economical solutions for the injection moulding process. Thanks to its comprehensive knowledge of materials, GÜNTHER is able to offer its customers technically sophisticated manifold systems, which promise optimum results thanks to high-quality surfaces in the melt channels and by taking the respective plastic properties into account. GÜNTHER carries out material tests under production conditions in its technical centre among other measures. To ensure homogeneous temperature distribution over the entire manifold, GÜNTHER utilises thermal simulations in the constructive design of its manifolds. These results flow directly into the technical implementation of customer-specific manifolds.
Visitors to the K 2019, The World’s No. 1 Trade Fair for Plastics and Rubber, from October 16-23, 2019 in Düsseldorf can discover the advantages of GÜNTHER manifold technology first hand in Hall 1 / Stand C44.
All melt-conducting manifold elements are heated externally, which ensures optimum melt flow with the smallest possible pressure loss. Pressed-in heaters on both sides using specially designed groove geometry ensure optimum heat transfer to the manifold block. Depending on the customer’s request or requirement, the manifold can be soldered, or diffusion welded. Diffusion welding offers the advantage of no additional solder being needed, which can escape during the soldering process and enter the manifold channel. As a consequence, additional surface treatment can be avoided, and gentle melt flow achieved. By joining two manifold halves, there are no undercuts or edges in the melt channels, which could lead to increased shear and thus to varied flow behaviour of the melt. Introducing the melt channels in two manifold halves increases the design possibilities for balancing the channels, allowing even for the design of fully balanced, complex systems.
The greatest amount of wear usually takes place in the deflections, since here the melt is diverted in a different direction and thus subject to a variety of shear forces. For this purpose, GÜNTHER offers technically sophisticated deflecting units in its portfolio that can be used to fulfil corresponding requirements. The new split standard deflectors offer numerous advantages in terms of flow, such as high-precision surfaces of the melt channels, and also offer the practical advantage of being able to be easily and quickly changed when worn or for cleaning. In addition to deflectors, plugs for closing the high-quality drilled manifold channels are of vital importance. For this, GÜNTHER relies on its comprehensive range of plugs. Inclined plugs or contour plugs move the melt through their surface geometry more gently, while still providing sufficient access to the melt channel during cleaning. Contour plugs for valve gate applications and open systems are also available.
Other innovations at the K
At the K 2019, GÜNTHER will also be presenting other innovations in addition to its innovative cold runner technology and intelligent manifold technology. With the launch of the BlueFlow® hot runner nozzle, Günther set new standards in terms of energy-saving and a particularly slim nozzle design at the K2010. Now, nine years after first presenting the “Blue Nozzle,” innovations in the BlueFlow® product range will be presented at the trade fair for the first time.
As part of the K, GÜNTHER will also be presenting the relaunch of the CADHOC® System Designer, the configuration program for individual components and complete hot runner systems. User suggestions have been collected in recent years and are now reflected in the relaunch. Not only has the usability of the configuration program been improved, but new save functions for configurations have also been introduced. This ensures that users can always access completed configurations and can use them as a template for new designs as needed. Additional features of the CADHOC® System Designer will be presented to the public at the K.
Visit GÜNTHER in Düsseldorf at the K in Hall 1 – Stand C44.
GÜNTHER UK Limited
01474 879774
Website
Email