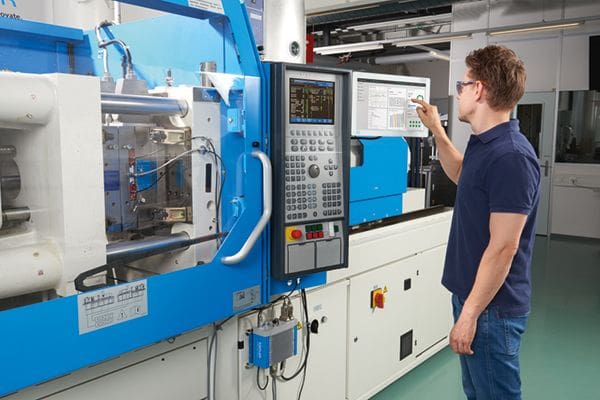
Kistler Instruments to Showcase ComoNeo – The Next Generation at PDM 2018
On Stand B029 at PDM 2018, Kistler Instruments will be showing the latest version of its ComoNeo cavity pressure monitoring system with enhanced capability to meet the needs of today’s injection moulding industry.
Easily configured to meet specific user needs with up to 32 inputs for piezoelectric cavity pressure sensors, 16 inputs for temperature measurement and 4 analogue voltage channels for machine signals, such as screw position and machine pressure, moves automated production process monitoring into a whole new dimension. The ComoNeo is the system of choice for any injection moulding company that aims to optimize monitoring and analysis of the moulding process to permanently cut costs by increasing productivity and removing defects at the earliest stage in the production process.
Easy to operate, ComoNeo monitors the profile of cavity pressure in real-time with graphical display makes it easy to identify process fluctuations. Integrated data storage allows recording of curve histories with at least 50 000 cycles. Curve superimposition and a host of other useful functions (changeable colour schemes to display curves, cycle comments, cursor functions, etc.) allow detailed analysis directly on the injection moulding machine.
Production mode includes clear displays showing production progress and scrap rate, as well as intelligent mechanisms (e.g. automatic detection of interruptions to production and declaration of a defined number of cycles as scrap on restarting). As well as part quality, ComoNeo can monitor process stability and give warning signals in case of process fluctuations.
The design of the software is predicated on operational simplicity by using advanced technology to minimising the need for manual input. Typically, the integrated software automatically generates and positions the monitoring boxes for good/bad evaluation which, in the past, had to be set manually whilst an Evaluation Assistant systematically guides the user quickly and accurately to define the evaluation types and the relevant limits. In addition to making the initial setup faster and more accurate, this approach ensures that the production process is monitored with high precision, false rejects reduced and faulty components eliminated from production line. Reducing false rejects and eliminating out of spec products are the two most crucial factors in cutting production costs and increasing productivity in the injection moulding process.
The new overview screen, the “dashboard”, collates all the relevant process data to give a clear picture of how the current production is progressing allowing the user to detect process fluctuations very quickly. Users can also navigate directly from the dashboard to the detailed data and the operating controls and procedures are consistently geared to the injection moulding process, for instance, the performance of an individual cavity can be analysed.
Automatic mould identification reduces toolchange times and prevents errors on the interface between the mould and the ComoNeo system to maximize production efficiency in the injection moulding process whilst the new hardware and software allow more cavities to be monitored bringing automatic product quality assurance to large, multi-cavity operations whilst the new optimised touch screen display provides a comprehensive interface that can be adapted to meet specific operational needs.
The system may be expanded using the CoMoDataCenter to network all the ComoNeo devices allowing data to be viewed in real-time or as archived historical data. Where needed, the MultiFlow module may be integrated to provide automatic hot runner balancing based on the individual cavity pressure profile.
By ensuring maximum production efficiency and minimum reject rates, the new Kistler CoMoNeo monitoring system is the natural choice for quality conscious injection moulding companies which demand the highest standards of productivity and product quality. The objective of Kistler’s development of cavity pressure monitoring has always been the achievement of “Zero Defect” which the new CoMoNeo system now delivers at lower capital cost than other systems, including vision systems.
Kistler Instruments
+44 (0) 1256 741 550
Website
Email