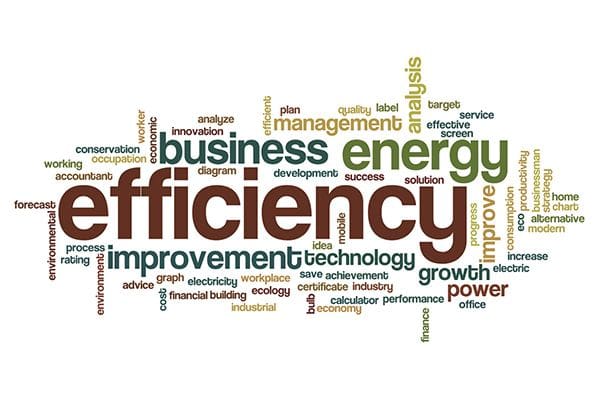
Wittmann Battenfeld UK Equipment to Show Energy Savings at Industry 4.0 Days
Visitors to Wittmann Battenfeld UK’s (WIBA UK) Industry 4.0 days this April 24th and 25th will also be able to assess the energy saving performances of all equipment on demonstration.
WIBA UK customer, Oxfordshire-based Injection moulding innovator White Horse Plastics (WHP), is currently reaping the benefit of an intense focus on the business’s current energy consumption and savings.
WHP Factory Manager Paul Bobby says that ‘after labour and raw material costs, energy and utilities present WHP with the next most significant overhead. Accordingly, we have made electricity consumption one of our key business focuses for the coming year.’
One of the first 2018 objectives WHP set itself was to better understand the true cost of energy consumption across all the entire WHP plant and factory. The main contributors such as injection moulding machines (IMM) were assessed first, together with the main ancillaries used in production, including material driers, tool-heaters, temperature controllers, hot-runners and other equipment.
Initially and with the assistance of WHP’s IMM partner, Wittmann Battenfeld, it was decided to evaluate some of the company’s older machine stock versus their latest Wittmann Battenfeld Smart-Power IMMs.
In order to get authentic and comparable data an energy logger was used to measure actual KWh consumed.
Injection Moulding Machine Study Summary:
Battenfeld HM 100/350 B4 (year 2000) v Wittmann Battenfeld Smart-Power 90 (year 2016)
- Tool selected: 8 impression damper Cap
- Material: 30% Glass Filled PA 6.6
- Cycle: 16 seconds
- Material usage: 8 Kg per hour
- Trial period: 6 hours
- Total Kwh used: HM 100 = 43.5 Kwh Smart-Power 90 = 8.65 Kwh
- Average Kwh/hr: HM 100 = 6.8 Kwh Smart-Power 90 = 1.21 Kwh
Paul Bobby says that ‘I always expected to see some significant improvement when comparing old to new. However, these outcomes were far more impressive than could ever have been hoped for.
In fact,’ he adds, ‘the greatly reduced running costs from the Smart-Power machine were so incredible that it led to us repeating the exercise in order to check our methodology. However, when repeated these results were exactly the same.’
The outcomes of the WHP energy measurement exercises have now focussed the company mind on the energy-saving potential future for the business as a whole. Bobby says that ‘WHP purchasing strategy will now change – and where existing plant is to be replaced, energy efficiency will now be considered equally with technical processing specifications.’
In this pilot exercise Wittmann Battenfeld’s injection moulding equipment certainly passed with flying colours. ‘The machines are called SmartPower for a very good reason,’ says Bobby ‘and the energy savings achieved are truly world class.’
About WHP (White Horse Plastics) Ltd
WHP Ltd specialises in the development and production of tight tolerance technical injection mouldings and sub assemblies, using materials ranging from standard polymers, nylons, acetals, polycarbonates, ABS and TPEs etc through to the more exotic engineering polymers.
WHP Ltd has over forty years of experience tackling the most challenging aspects of technical moulding. Its mission and objective is always to provide complete manufacturing solutions for its clients.
The company is located in the Vale of the White Horse in Stanford-in-the-Vale, mid-distance between Swindon and Oxford. The business was founded in 1973 and its current technical competencies include a fleet of over thirty injection moulding machines; CAD/CAM facilities, CNC optical measurement, CMM systems, insert loading and camera inspection, a fully equipped tool room and dedicated med-tech manufacturing space.
In addition to ISO9001, the environmental standard ISO 14001 and the automotive quality standard TS 16949, WHP recently achieved (August 2016) the ISO 13485 for the production of medical devices.
Wittmann Battenfeld
+44 (0) 1933 275777
Website
Email