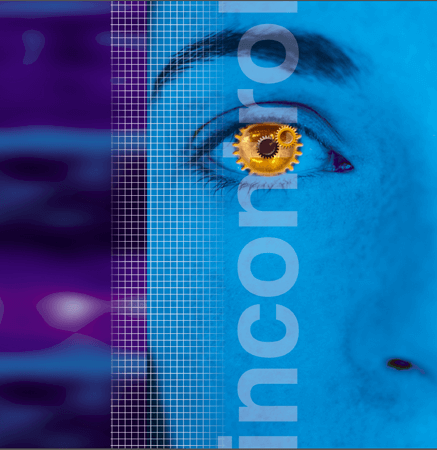
Intouch Monitoring Increase Profitability for OnePlastics Group
OnePlastics Group, one of the world’s fastest growing plastic manufacturing companies, implemented Intouch Monitoring 7 years ago on over 30 production machines in its manufacturing plant in Tamworth.
As a direct result it has “without question increased our profitability”, according to Dave Sheridan, Operations Manager at OnePlastics. One of their blue chip customers quoted: “The (Intouch) system gives you the point of difference compared to other suppliers.”
Dave Sheridan continued:
“At high level, Intouch has provided the information needed on OEE for us to make decisions on where Capex should be prioritised to increase ‘up time’ and quality of product. Intouch has provided us information on scrap, downtime and trends that has significantly contributed to our continuous improvement programs. We have reduced scrap by 1.4% across the sites by pin pointing the ‘actual’ scrap reasons and then working to resolve the cause of it. We use the scheduling Gantt Chart not only to schedule jobs but equally important plan equipment servicing. This along with the down time reporting, has helped us concentrate on problematic areas – be it equipment, labour shortage or down time related to running out of bought out materials.
“Uptime has improved across the site by 10%! The Gantt Chart helps the team prepare for the Next Change. We have improved changeover times in some cells by 30%.
“This is really important as we have over 170 changes across the site per week. All of this without question increased our profitability of the business. Intouch has helped us win new business.”
Intouch Monitoring
+44 (0) 1604 646144
Website
Email